When the mechanical rotor is running, the unbalanced inertia force generated by the component will cause additional dynamic pressure in the pair. This not only increases friction in the range of motion and internal stress in the member, but also reduces mechanical efficiency and service life. Moreover, since the magnitude and direction of these inertial forces are generally periodic, they will inevitably cause forced vibration of the machine and its foundation. If its amplitude is large, or its frequency is close to the mechanical resonance frequency, it will cause extremely bad consequences. It will not only affect the normal operation and service life of the machine itself, but also affect or even destroy the nearby plant machinery and building.
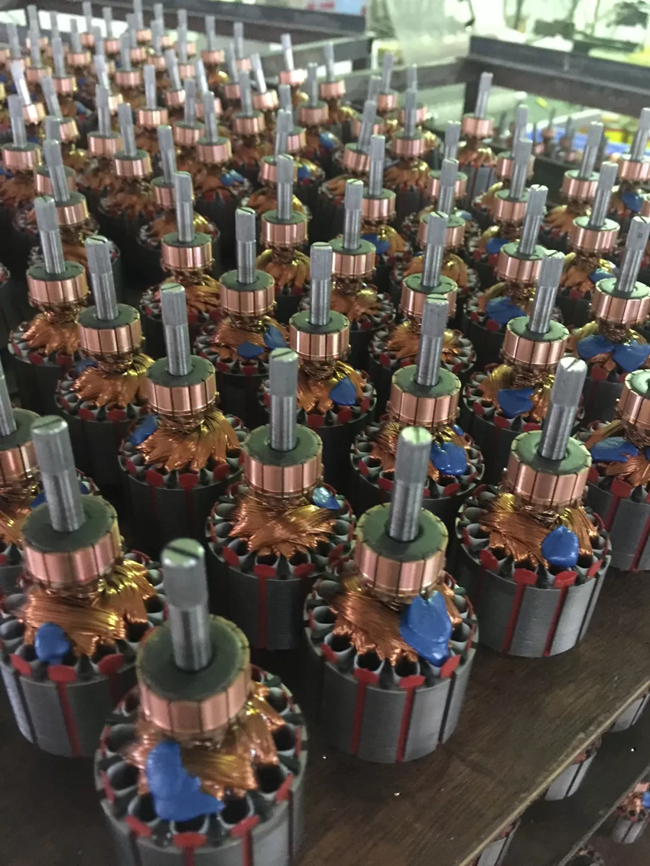
1. The purpose of dynamic balance correction of mechanical rotor: when the machine is running, the unbalanced inertia force produced by the component will cause additional dynamic pressure in the motion pair. This will not only increase the friction in the amplitude of motion and the internal stress in the member, but also reduce the mechanical efficiency and service life. Since the magnitude and direction of these inertial forces are generally periodic, they will inevitably cause forced vibration of the machine and its foundation. If its amplitude is large, or its frequency is close to the mechanical resonance frequency, it will cause extremely bad consequences. It will not only affect the normal operation and service life of the machine itself, but also affect or even destroy the nearby plant machinery and building.
The purpose of dynamic balance correction of mechanical rotor is to balance the unbalanced inertial force of components so as to eliminate or reduce the harmful influence of inertial force. However, it should be pointed out that some machines work by means of vibration caused by unbalanced inertia force generated by components, such as compactor, massage machine, vibration pile driver, vibration transporter, etc.
2. Content of dynamic balance of mechanical rotor: In machinery, inertia force and balance method are different due to different structure and movement form of components. Accordingly, the problems of mechanical balance can be divided into the following two categories.
3. Inertia force balance of components rotating around fixed shaft:
(1) Balance of rigid rotor: In general machinery, the rigidity of the rotor is better, the resonance speed is higher, and the working speed of the rotor is lower than (0.6 0.75) (the first resonance speed of the rotor). At this time, the elastic deformation of the rotor is very small. This kind of rotor is called rigid rotor. If only its inertial force balance is required, it is called rotor static balance. If the balance of inertia force and moment is required at the same time, it is called dynamic balance of rotor.
(2) Balance of winding rotors: Rotor balance with operating speed greater than the first-order critical speed. Some machines, such as turbo engines, have large mass and span, but small radial dimensions. Therefore, the resonance speed is low. If the operating speed is greater than (0.6~0.75), the rotor will be deformed greatly during operation, which will significantly increase the inertial force. This type of rotor is called a winding rotor.
3. Balance of mechanism: generally refers to the balance of mechanism with reciprocating movement or plane compound moving member. Inertia force and moment of inertia can not eliminate all inertia forces and moments of inertia on all components inside the member and can be combined into a total inertia force and moment of inertia acting on the frame through the center of mass of the mechanism.
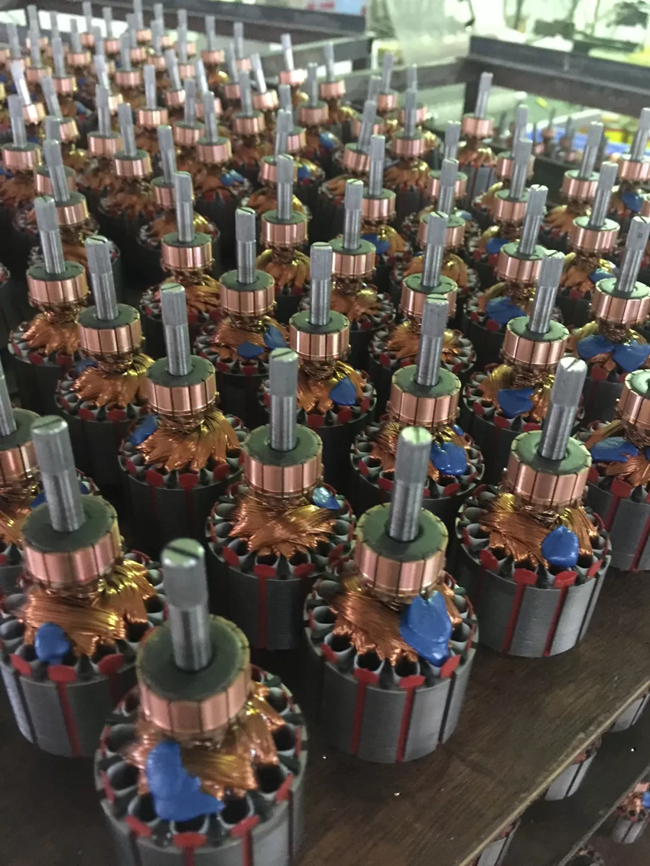
1. The purpose of dynamic balance correction of mechanical rotor: when the machine is running, the unbalanced inertia force produced by the component will cause additional dynamic pressure in the motion pair. This will not only increase the friction in the amplitude of motion and the internal stress in the member, but also reduce the mechanical efficiency and service life. Since the magnitude and direction of these inertial forces are generally periodic, they will inevitably cause forced vibration of the machine and its foundation. If its amplitude is large, or its frequency is close to the mechanical resonance frequency, it will cause extremely bad consequences. It will not only affect the normal operation and service life of the machine itself, but also affect or even destroy the nearby plant machinery and building.
The purpose of dynamic balance correction of mechanical rotor is to balance the unbalanced inertial force of components so as to eliminate or reduce the harmful influence of inertial force. However, it should be pointed out that some machines work by means of vibration caused by unbalanced inertia force generated by components, such as compactor, massage machine, vibration pile driver, vibration transporter, etc.
2. Content of dynamic balance of mechanical rotor: In machinery, inertia force and balance method are different due to different structure and movement form of components. Accordingly, the problems of mechanical balance can be divided into the following two categories.
3. Inertia force balance of components rotating around fixed shaft:
(1) Balance of rigid rotor: In general machinery, the rigidity of the rotor is better, the resonance speed is higher, and the working speed of the rotor is lower than (0.6 0.75) (the first resonance speed of the rotor). At this time, the elastic deformation of the rotor is very small. This kind of rotor is called rigid rotor. If only its inertial force balance is required, it is called rotor static balance. If the balance of inertia force and moment is required at the same time, it is called dynamic balance of rotor.
(2) Balance of winding rotors: Rotor balance with operating speed greater than the first-order critical speed. Some machines, such as turbo engines, have large mass and span, but small radial dimensions. Therefore, the resonance speed is low. If the operating speed is greater than (0.6~0.75), the rotor will be deformed greatly during operation, which will significantly increase the inertial force. This type of rotor is called a winding rotor.
3. Balance of mechanism: generally refers to the balance of mechanism with reciprocating movement or plane compound moving member. Inertia force and moment of inertia can not eliminate all inertia forces and moments of inertia on all components inside the member and can be combined into a total inertia force and moment of inertia acting on the frame through the center of mass of the mechanism.
232 browse