The sensor of dynamic balancing machine is the most important link to realize automatic detection and control. It plays an important role in the rotor dynamic balancing test system. It can transform the detected information into electrical signal or other information output according to the information characteristics. Huake Zhi, a technician of dynamic balancing machine, focuses on introducing the types of sensors of dynamic balancing machine.
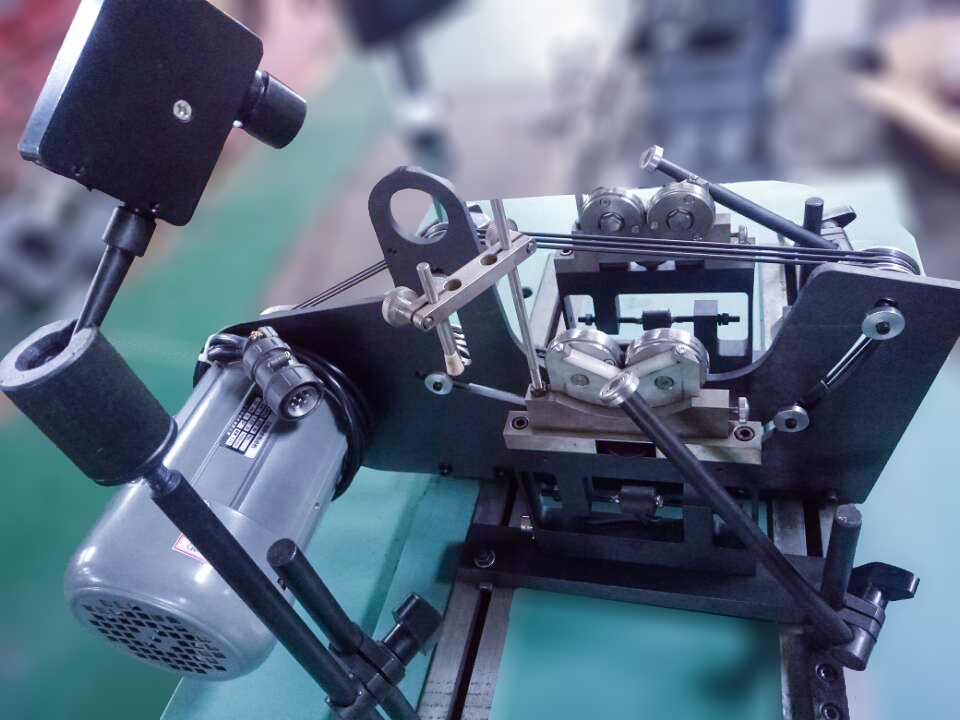
The working principle of the vibration signal detected by the sensor can be represented by three processes: the first process is to accept the vibration signal, the second process is to convert the vibration signal into electrical signal, and the third process is to convert the electrical signal into voltage signal that can be processed by the following instrument. There are many kinds of sensors in practical application, such as pressure sensor, infrared sensor, displacement sensor, photoelectric sensor and so on. Here, several vibration sensors used in rotor dynamic balance maneuvering balance test system are emphatically introduced.
1. Speed Sensor
A speed sensor is a sensor that converts the speed at which an object vibrates into an electrical output. It is a non-contact measuring device, which can be manufactured by mechanical, electrical, magnetic, optical and hybrid methods. Common speed sensors are divided into magnetic inductive type, photoelectric effect type and Hall effect type. Its advantages are easy installation, no need for external power supply, good performance in measuring medium frequency range, and suitable for medium speed rotors. The disadvantage is that the performance will degrade over a period of time and there will be a certain phase difference in low frequency prediction.
2. Acceleration sensor
The acceleration sensor is an electronic device which can measure the acceleration force. In physics, when an object is subjected to a force that generates an acceleration, such as gravity, the acceleration force can be a constant, such as g, or a variable. The acceleration sensor is designed according to this principle. Commonly used are magnetoelectric acceleration sensor, piezoelectric acceleration sensor and optical fiber acceleration sensor. In unbalanced measurement, piezoelectric acceleration sensor is common. Its advantage is good reliability, convenient installation and suitable for measuring high-frequency vibration. The disadvantage is that it is difficult to measure low frequency vibration and external DC power supply is required for measurement.
3. Speed Sensor
A speed sensor is a sensor that converts the speed of a rotating object into an electrical output. It accurately measures the instantaneous speeds of various motors used in automatic control systems and instruments. Commonly used speed sensors are magnetic inductive type, photoelectric effect type, reluctance effect type and capacitive type. The phase of the imbalance is based on the speed signal, and the periodic pulse signal of the speed measurement is also provided by the speed signal.
4. Displacement sensor
Displacement sensor is also called linear sensor. Common sensors include inductive displacement sensor, capacitive displacement sensor, photoelectric displacement sensor, ultrasonic displacement sensor and Hall displacement sensor. The working principle of the displacement sensor is to convert the physical displacement of the object to be measured into the corresponding electrical signal. Displacement sensors are mainly used for intelligent control of analog quantities in automatic equipment production lines. Its advantage is that the signal-to-noise ratio of the measured signal is high and the measuring frequency range is wide. It can directly measure the vibration position and is easy to calibrate it. The disadvantage is that it is inconvenient to install and needs external DC power supply when using.
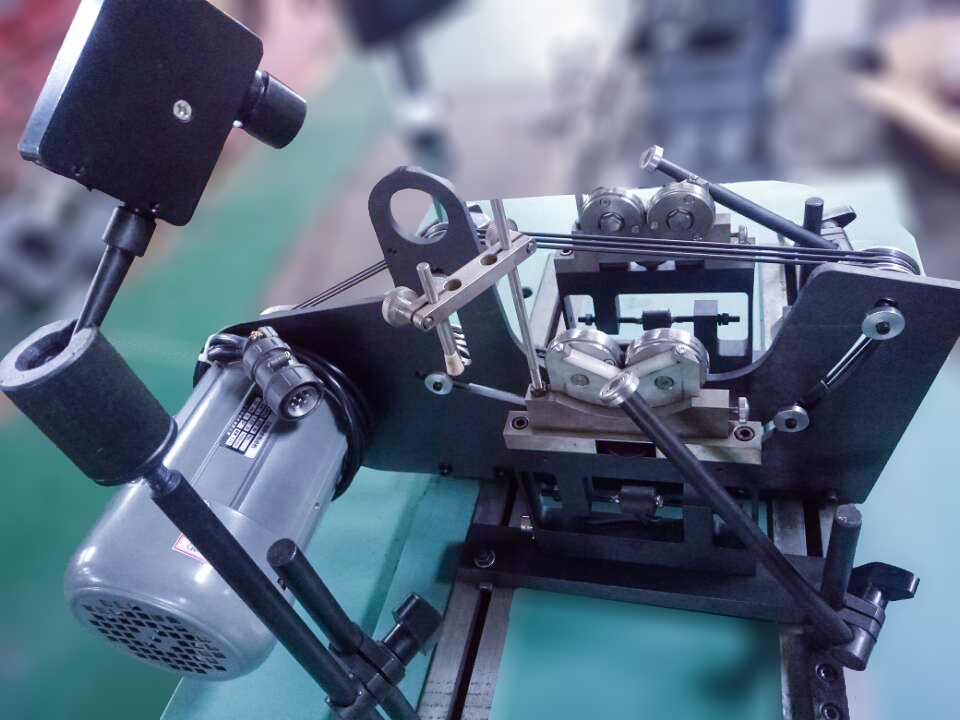
The working principle of the vibration signal detected by the sensor can be represented by three processes: the first process is to accept the vibration signal, the second process is to convert the vibration signal into electrical signal, and the third process is to convert the electrical signal into voltage signal that can be processed by the following instrument. There are many kinds of sensors in practical application, such as pressure sensor, infrared sensor, displacement sensor, photoelectric sensor and so on. Here, several vibration sensors used in rotor dynamic balance maneuvering balance test system are emphatically introduced.
1. Speed Sensor
A speed sensor is a sensor that converts the speed at which an object vibrates into an electrical output. It is a non-contact measuring device, which can be manufactured by mechanical, electrical, magnetic, optical and hybrid methods. Common speed sensors are divided into magnetic inductive type, photoelectric effect type and Hall effect type. Its advantages are easy installation, no need for external power supply, good performance in measuring medium frequency range, and suitable for medium speed rotors. The disadvantage is that the performance will degrade over a period of time and there will be a certain phase difference in low frequency prediction.
2. Acceleration sensor
The acceleration sensor is an electronic device which can measure the acceleration force. In physics, when an object is subjected to a force that generates an acceleration, such as gravity, the acceleration force can be a constant, such as g, or a variable. The acceleration sensor is designed according to this principle. Commonly used are magnetoelectric acceleration sensor, piezoelectric acceleration sensor and optical fiber acceleration sensor. In unbalanced measurement, piezoelectric acceleration sensor is common. Its advantage is good reliability, convenient installation and suitable for measuring high-frequency vibration. The disadvantage is that it is difficult to measure low frequency vibration and external DC power supply is required for measurement.
3. Speed Sensor
A speed sensor is a sensor that converts the speed of a rotating object into an electrical output. It accurately measures the instantaneous speeds of various motors used in automatic control systems and instruments. Commonly used speed sensors are magnetic inductive type, photoelectric effect type, reluctance effect type and capacitive type. The phase of the imbalance is based on the speed signal, and the periodic pulse signal of the speed measurement is also provided by the speed signal.
4. Displacement sensor
Displacement sensor is also called linear sensor. Common sensors include inductive displacement sensor, capacitive displacement sensor, photoelectric displacement sensor, ultrasonic displacement sensor and Hall displacement sensor. The working principle of the displacement sensor is to convert the physical displacement of the object to be measured into the corresponding electrical signal. Displacement sensors are mainly used for intelligent control of analog quantities in automatic equipment production lines. Its advantage is that the signal-to-noise ratio of the measured signal is high and the measuring frequency range is wide. It can directly measure the vibration position and is easy to calibrate it. The disadvantage is that it is inconvenient to install and needs external DC power supply when using.
239 browse