Key characteristics of vibration spectrum: The problem of rotor imbalance is generally characterized by high rotational frequency vibration occupying the core, and its rotational frequency vibration component usually exceeds or is equivalent to about 80% of its direct frequency vibration.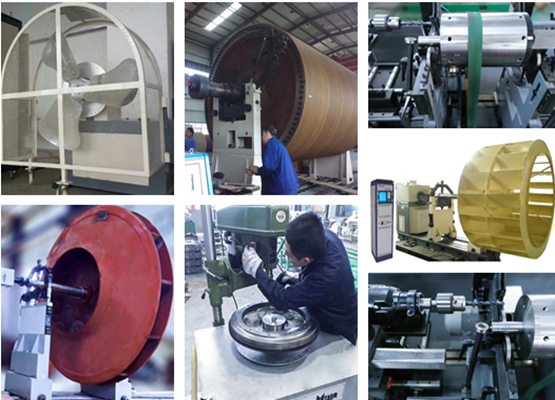
Unbalanced forces have necessary directionality, and centrifugal forces are uniform on a radial basis. The motion trajectory of the shaft and supporting bearings is similar to one circle. Obviously, because the vertical support stiffness of the bearing seat exceeds the horizontal direction, the normal motion trajectory of the shaft and supporting bearings is elliptical, which means that under normal circumstances, the horizontal vibration is 1.5 to 2 times greater than the vertical vibration. If this standard is exceeded, there will be other problems, There will be resonance issues very much.
Compared to axial vibration, when imbalance issues dominate, radial vibration (horizontal and vertical) is not significant compared to axial vibration (except for cantilever rotors).
The directionality of the imbalance problem of a cantilever rotor is generally characterized by large radial and axial vibrations, which exist together with static imbalance and couple imbalance. Therefore, it is generally necessary to use a two plane balance correction.
The rotor with imbalanced vibration problems has stable and identical vibration phases. Unbalance issues can promote the amplification of resonance amplitude. If the working speed of the rotor is closer to the resonance point at its system natural frequency, a small amount of unbalanced vibration will increase by 10 to 50 times.
The phase manifestation of rotor imbalance problem is that the phase difference detected in the horizontal direction of the rotor input and output bearings is the same as the phase difference measured in the vertical direction of the rotor input and output bearings (+/-30 °). Otherwise, the key issue is not dynamic balance problem. For example, if the vibration phase difference detected in the horizontal direction of the input and output bearings of a motor is 30 °, and the similarity of the vibration phase difference detected in the vertical direction of the input and output bearings is 150 °, then the technician's attempt to balance the rotor is like wasting time.
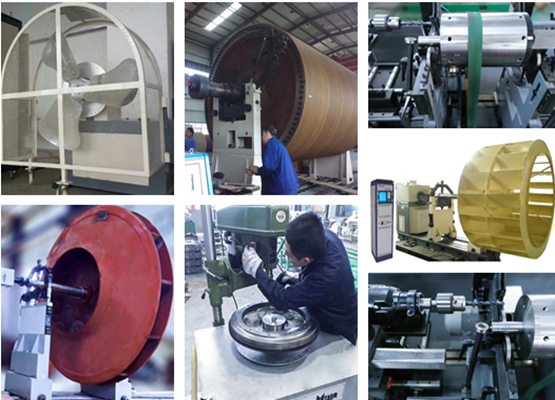
Unbalanced forces have necessary directionality, and centrifugal forces are uniform on a radial basis. The motion trajectory of the shaft and supporting bearings is similar to one circle. Obviously, because the vertical support stiffness of the bearing seat exceeds the horizontal direction, the normal motion trajectory of the shaft and supporting bearings is elliptical, which means that under normal circumstances, the horizontal vibration is 1.5 to 2 times greater than the vertical vibration. If this standard is exceeded, there will be other problems, There will be resonance issues very much.
Compared to axial vibration, when imbalance issues dominate, radial vibration (horizontal and vertical) is not significant compared to axial vibration (except for cantilever rotors).
The directionality of the imbalance problem of a cantilever rotor is generally characterized by large radial and axial vibrations, which exist together with static imbalance and couple imbalance. Therefore, it is generally necessary to use a two plane balance correction.
The rotor with imbalanced vibration problems has stable and identical vibration phases. Unbalance issues can promote the amplification of resonance amplitude. If the working speed of the rotor is closer to the resonance point at its system natural frequency, a small amount of unbalanced vibration will increase by 10 to 50 times.
The phase manifestation of rotor imbalance problem is that the phase difference detected in the horizontal direction of the rotor input and output bearings is the same as the phase difference measured in the vertical direction of the rotor input and output bearings (+/-30 °). Otherwise, the key issue is not dynamic balance problem. For example, if the vibration phase difference detected in the horizontal direction of the input and output bearings of a motor is 30 °, and the similarity of the vibration phase difference detected in the vertical direction of the input and output bearings is 150 °, then the technician's attempt to balance the rotor is like wasting time.
233 browse