A common measure to reduce the axial force borne by the impeller of a centrifugal pump is to install a sealing ring and a balance hole structure on the outer side of the rear cover plate of the centrifugal impeller. Based on the pressure distribution law of rotating fluid, this article quantitatively calculates the leakage of the structure through mathematical analysis, derives the theoretical formula for calculating axial force, and proves that the structure can achieve the goal of reducing axial force. The research results help to avoid blindness in the design of impeller balancing mechanisms and provide reference for correctly determining the relevant geometric dimensions of impellers.
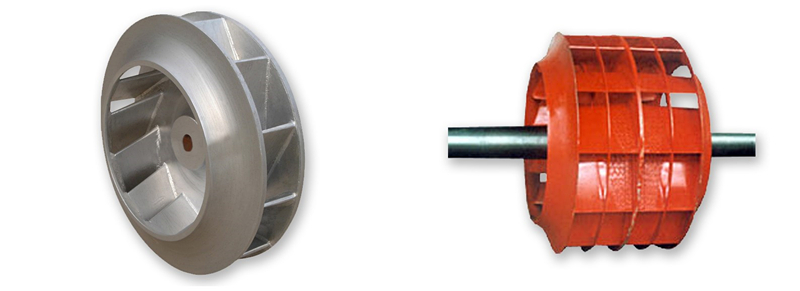
A high-performance centrifugal pump should not only have good hydraulic performance, but also have an expected service life. In some continuously operating production lines, such as the chemical and metallurgical industries, customers' requirements for the reliability of key equipment have even become the main indicator for selecting equipment. The force state of centrifugal pump components is complex, and some components can experience high orders of magnitude of external forces. This is the main reason why some components of the pump, such as bearings, seals, and keys, fail prematurely and seriously shorten the maintenance cycle of the pump. So, the high-speed rotating impeller must undergo dynamic balance correction.
After the liquid flows through the impeller, the mechanical energy of the fluid increases due to the work done by the impeller, and the main form of this increased energy is pressure energy. The high pressure at the impeller outlet forms an axial distributed force system acting on the outer side of the impeller front and rear cover plates in a certain distribution pattern in the front and rear pump chambers of the pump. Due to the asymmetry of the front and rear cover plate structures, the opposite axial forces on the outer sides of the front and rear cover plates cannot be balanced with each other, resulting in axial forces acting in the direction of the impeller suction port. In high head low specific speed pumps or large-sized pumps, this axial force cannot be ignored. There are various hydraulic methods to reduce the axial force on the impeller. Setting balance holes and sealing rings on the rear cover plate of the impeller is a common method to achieve this goal; However, for a long time, designers' understanding of this effective structure has remained mostly qualitative, and so far there has been no quantitative analysis of its effect on reducing axial force.
Centrifugal impellers can experience imbalance during use for various reasons, such as wear and scaling. Whether using impellers treated with thermal spraying or using various methods to remove scale, the effect will not be permanent. After long-term use, there may still be vibrations exceeding the allowable upper limit order. At this point, the imbalance problem of the impeller can only be solved through dynamic balance correction.
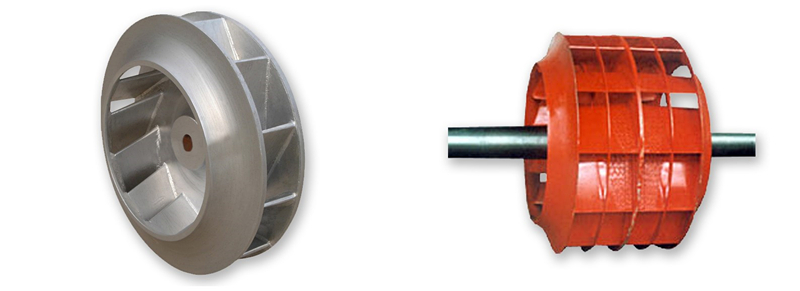
A high-performance centrifugal pump should not only have good hydraulic performance, but also have an expected service life. In some continuously operating production lines, such as the chemical and metallurgical industries, customers' requirements for the reliability of key equipment have even become the main indicator for selecting equipment. The force state of centrifugal pump components is complex, and some components can experience high orders of magnitude of external forces. This is the main reason why some components of the pump, such as bearings, seals, and keys, fail prematurely and seriously shorten the maintenance cycle of the pump. So, the high-speed rotating impeller must undergo dynamic balance correction.
After the liquid flows through the impeller, the mechanical energy of the fluid increases due to the work done by the impeller, and the main form of this increased energy is pressure energy. The high pressure at the impeller outlet forms an axial distributed force system acting on the outer side of the impeller front and rear cover plates in a certain distribution pattern in the front and rear pump chambers of the pump. Due to the asymmetry of the front and rear cover plate structures, the opposite axial forces on the outer sides of the front and rear cover plates cannot be balanced with each other, resulting in axial forces acting in the direction of the impeller suction port. In high head low specific speed pumps or large-sized pumps, this axial force cannot be ignored. There are various hydraulic methods to reduce the axial force on the impeller. Setting balance holes and sealing rings on the rear cover plate of the impeller is a common method to achieve this goal; However, for a long time, designers' understanding of this effective structure has remained mostly qualitative, and so far there has been no quantitative analysis of its effect on reducing axial force.
Centrifugal impellers can experience imbalance during use for various reasons, such as wear and scaling. Whether using impellers treated with thermal spraying or using various methods to remove scale, the effect will not be permanent. After long-term use, there may still be vibrations exceeding the allowable upper limit order. At this point, the imbalance problem of the impeller can only be solved through dynamic balance correction.
142 browse