In modern design, the crankshaft speed in the engine needs to be continuously increased to meet the demands of the engine. However, during the overall processing, there may be a phenomenon of center deviation caused by external factors, resulting in significant vibration during work, and ultimately leading to imbalance when the speed increases. To solve the balance problem, it is necessary to control the automatic crankshaft balancing machine.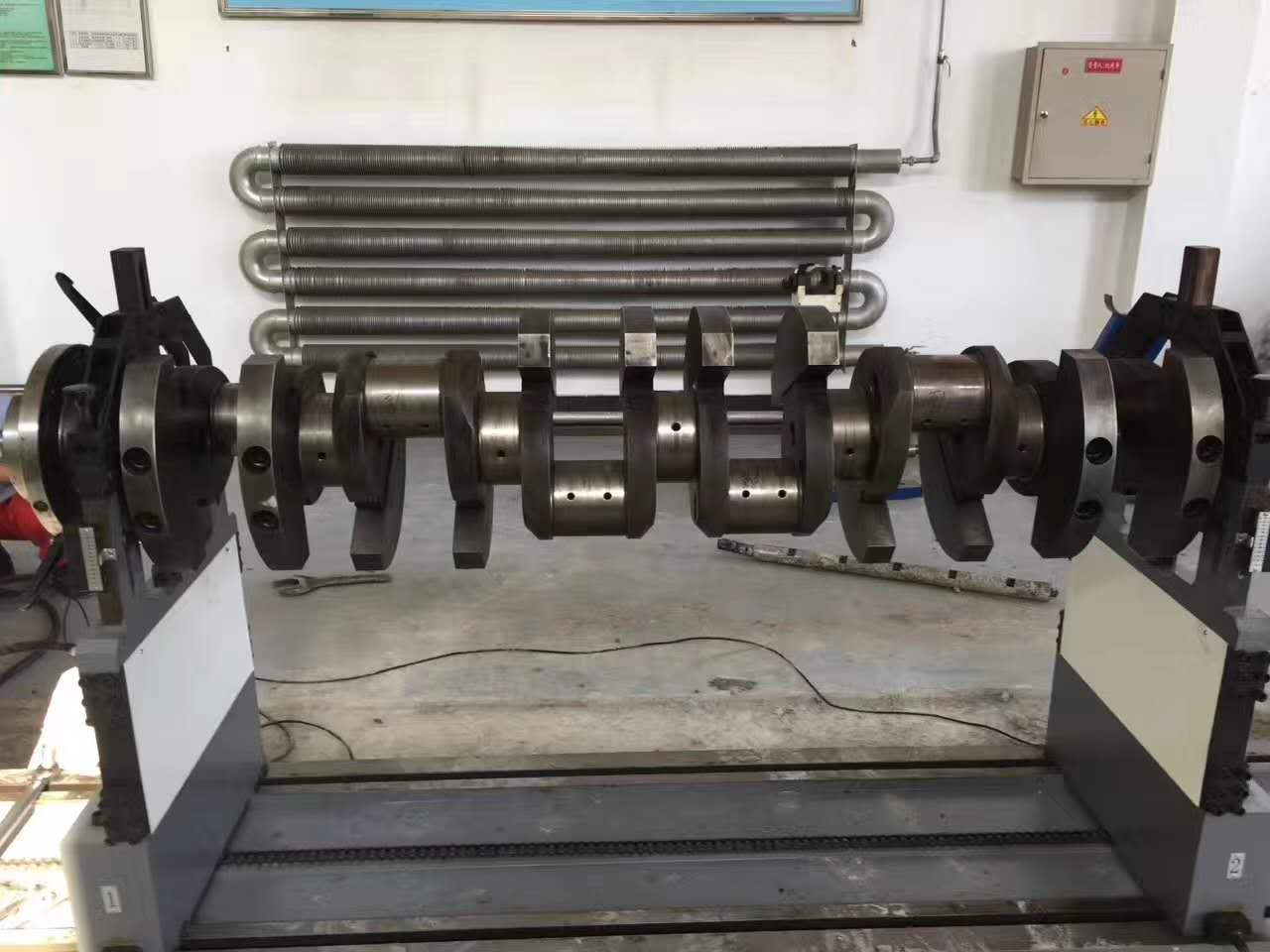
With the continuous development of modern technology, the role of the crankshaft in industrial production is quite significant, especially in the application and development of increasing power and speed of diesel engines. Therefore, in this situation, the crankshaft speed is also constantly increasing. On this basis, it is necessary to analyze and master the mechanized system of the balancing machine, and achieve its debugging through certain means. The technical specialist of Huake Zhichuang Dynamic Balancing Machine first provided an overview of the automatic crankshaft dynamic balancing machine, and then conducted research on the design and debugging of the mechanical system.
1、 Introduction to the Performance and Advantages of Automatic Crankshaft Dynamic Balancing Machine
In the composition structure of an automatic crankshaft dynamic balancing machine, it can be mainly divided into a drive system, a swing frame system, a microelectromechanical measurement system, a hydraulic system, and a cooling and lubrication system. The equipment drive system is mainly composed of the servo control unit, its matching servo motor, and transformer. The toothed synchronous belt transmission components can be effectively connected to the drive head and crankshaft parts in the frame through installation. In the swing frame system, it mainly relies on its driving spindle to fix its components in the frame, thereby driving the transmission through the action of its motor. In microelectromechanical measurement systems, point signals measured from sensors are processed and transmitted, requiring practical differentiation and filtering of various interference signals. In the entire mechanical system structure, it is mainly the control system that responds to its signals. The piston in the bracket oil cylinder will rise, thereby acting on the bracket oil shaft and causing the eccentric wheel to rotate. If it rises to a certain height during the rotation of the eccentric wheel, the front end of the bracket plate will rise. At this time, it is necessary to place the crankshaft in the bracket plate and achieve internal connection by installing and fixing it.
When conducting measurements, it is necessary to make effective allocation of the unbalanced force signals generated, among which the unbalanced signal converted to the right end will cause the phenomenon of relatively large vibration amplitude on the right side, thus generating a certain analysis of the unbalanced signal. In the overall measurement system, it is necessary to compare and analyze its signal with the reference signal, compare the unbalanced values and phases, and continuously test the machine tool after a series of adjustments until it is qualified.
2、 Research on the Design and Debugging of Mechanical Systems
When analyzing the design and debugging of mechanical systems, it is necessary to continuously analyze them based on balance mechanics. If numerical errors occur during the measurement process, strict analysis of the numerical errors needs to be conducted. The main reason for this phenomenon is the imbalance caused by the spindle system. When analyzing the spindle system, it is necessary to design and analyze the components that rotate together. If it is in an unbalanced state, the measured results will also be unbalanced. Therefore, when calculating it, it is necessary to analyze and calculate the imbalance in the right front side of the crankshaft, so as to fully analyze the imbalance force in the left and right front sides.
In terms of parameter selection for the system, it is necessary to analyze it according to the actual situation, continuously design and adjust it according to the user's needs, select suitable force sensors based on the actual situation, and make timely analysis and grasp of the deviation phenomena that occur.
In the process of adjusting its mechanical system, it is mainly based on the size of its parameters. Therefore, in this process, it is necessary to use theoretical calculation numerical parameters as reference conditions to analyze the bearing capacity of the supporting spring rod. After adjusting its stiffness, an effective budget is made for the actual values, so that the values presented in the principle can meet its relevant requirements within a certain error range. In terms of adjusting the transmission device, it is necessary to combine the synchronous motor, motor bracket, driving wheel, driven wheel, tension wheel, and synchronous belt into eight parts. Therefore, when making adjustments, the main starting point should be the driving wheel and driven wheel, so as to be in the same vertical plane as the workpiece axis. By adjusting the tension wheel, the degree of tightness of the synchronous belt can be analyzed and understood, and ultimately the interference caused by this part on the measurement results can be minimized. When adjusting the spindle system, it is necessary to use its careful adjustment method to ensure that the left and right balance weights in the main system are in a balanced state. Finally, when adjusting the mechanical amplifier and sensor, it is necessary to keep them in a free state and connect them to the frame without being affected by frame vibration phenomena.
In summary, in order to improve the automation level of the crankshaft mechanical crankshaft balancing machine, it is necessary to apply some special structures to its structure on the basis of practice, apply theory in practice, and ultimately ensure that the research and development of its automatic crankshaft balancing machine can provide comprehensive ways and methods for China's dynamic balancing field, ultimately promoting the development of industrial machinery in China.
The specific process of crankshaft dynamic balance correction depends on the number of machining, and the entire process is quite complex. Below is a detailed analysis of the Huake Zhichuang dynamic balance machine. The crankshaft rotates at high speed during operation. If the balance is not good, it will produce momentum peaks, and in severe cases, it can break. Generally, it is tested through a dynamic balancing machine to reduce some materials in the non stressed parts of the crankshaft. All high-speed rotating parts need to undergo balance testing, such as flywheels, transmission shafts, high-speed spindles, etc.
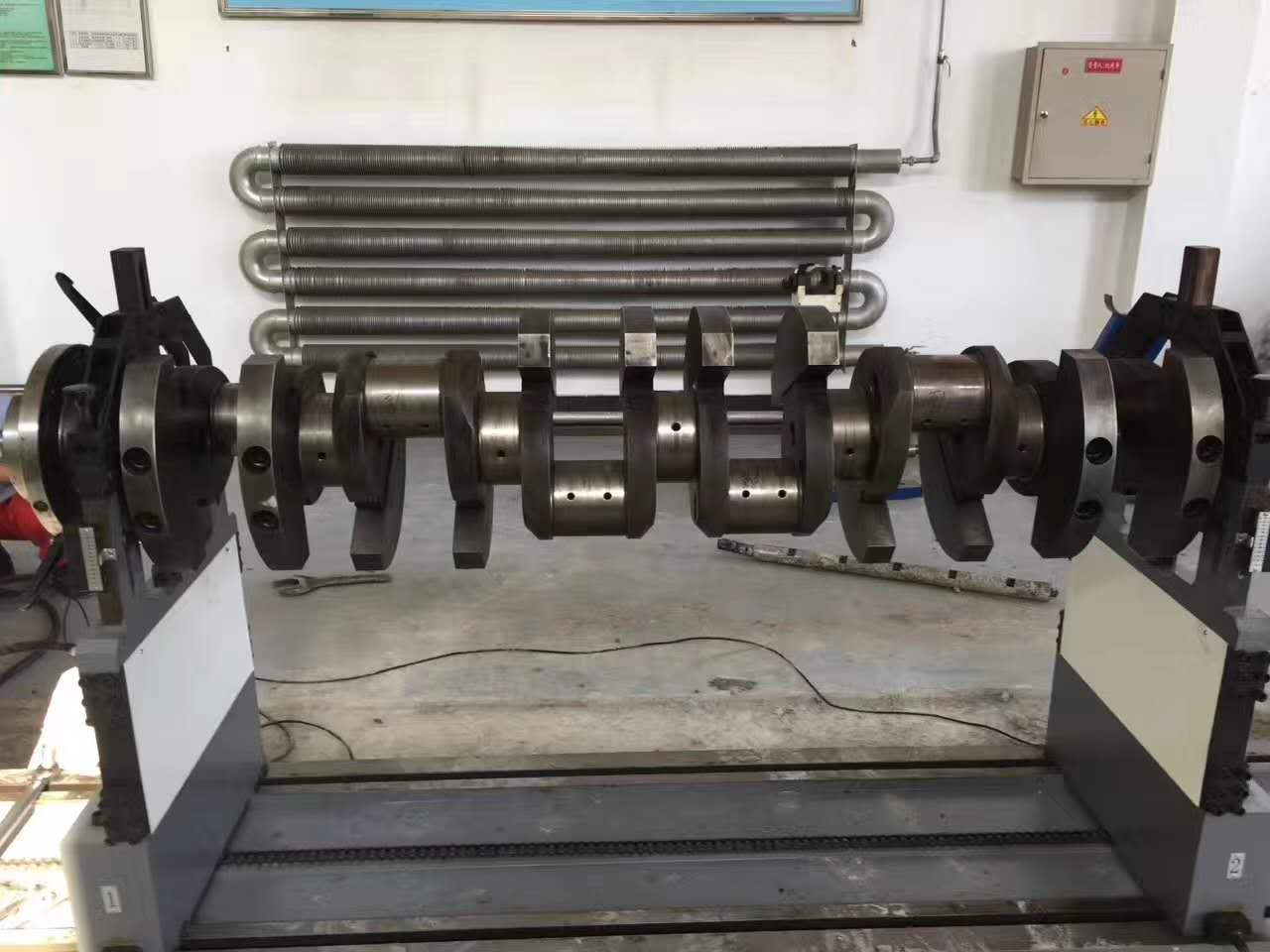
With the continuous development of modern technology, the role of the crankshaft in industrial production is quite significant, especially in the application and development of increasing power and speed of diesel engines. Therefore, in this situation, the crankshaft speed is also constantly increasing. On this basis, it is necessary to analyze and master the mechanized system of the balancing machine, and achieve its debugging through certain means. The technical specialist of Huake Zhichuang Dynamic Balancing Machine first provided an overview of the automatic crankshaft dynamic balancing machine, and then conducted research on the design and debugging of the mechanical system.
1、 Introduction to the Performance and Advantages of Automatic Crankshaft Dynamic Balancing Machine
In the composition structure of an automatic crankshaft dynamic balancing machine, it can be mainly divided into a drive system, a swing frame system, a microelectromechanical measurement system, a hydraulic system, and a cooling and lubrication system. The equipment drive system is mainly composed of the servo control unit, its matching servo motor, and transformer. The toothed synchronous belt transmission components can be effectively connected to the drive head and crankshaft parts in the frame through installation. In the swing frame system, it mainly relies on its driving spindle to fix its components in the frame, thereby driving the transmission through the action of its motor. In microelectromechanical measurement systems, point signals measured from sensors are processed and transmitted, requiring practical differentiation and filtering of various interference signals. In the entire mechanical system structure, it is mainly the control system that responds to its signals. The piston in the bracket oil cylinder will rise, thereby acting on the bracket oil shaft and causing the eccentric wheel to rotate. If it rises to a certain height during the rotation of the eccentric wheel, the front end of the bracket plate will rise. At this time, it is necessary to place the crankshaft in the bracket plate and achieve internal connection by installing and fixing it.
When conducting measurements, it is necessary to make effective allocation of the unbalanced force signals generated, among which the unbalanced signal converted to the right end will cause the phenomenon of relatively large vibration amplitude on the right side, thus generating a certain analysis of the unbalanced signal. In the overall measurement system, it is necessary to compare and analyze its signal with the reference signal, compare the unbalanced values and phases, and continuously test the machine tool after a series of adjustments until it is qualified.
2、 Research on the Design and Debugging of Mechanical Systems
When analyzing the design and debugging of mechanical systems, it is necessary to continuously analyze them based on balance mechanics. If numerical errors occur during the measurement process, strict analysis of the numerical errors needs to be conducted. The main reason for this phenomenon is the imbalance caused by the spindle system. When analyzing the spindle system, it is necessary to design and analyze the components that rotate together. If it is in an unbalanced state, the measured results will also be unbalanced. Therefore, when calculating it, it is necessary to analyze and calculate the imbalance in the right front side of the crankshaft, so as to fully analyze the imbalance force in the left and right front sides.
In terms of parameter selection for the system, it is necessary to analyze it according to the actual situation, continuously design and adjust it according to the user's needs, select suitable force sensors based on the actual situation, and make timely analysis and grasp of the deviation phenomena that occur.
In the process of adjusting its mechanical system, it is mainly based on the size of its parameters. Therefore, in this process, it is necessary to use theoretical calculation numerical parameters as reference conditions to analyze the bearing capacity of the supporting spring rod. After adjusting its stiffness, an effective budget is made for the actual values, so that the values presented in the principle can meet its relevant requirements within a certain error range. In terms of adjusting the transmission device, it is necessary to combine the synchronous motor, motor bracket, driving wheel, driven wheel, tension wheel, and synchronous belt into eight parts. Therefore, when making adjustments, the main starting point should be the driving wheel and driven wheel, so as to be in the same vertical plane as the workpiece axis. By adjusting the tension wheel, the degree of tightness of the synchronous belt can be analyzed and understood, and ultimately the interference caused by this part on the measurement results can be minimized. When adjusting the spindle system, it is necessary to use its careful adjustment method to ensure that the left and right balance weights in the main system are in a balanced state. Finally, when adjusting the mechanical amplifier and sensor, it is necessary to keep them in a free state and connect them to the frame without being affected by frame vibration phenomena.
In summary, in order to improve the automation level of the crankshaft mechanical crankshaft balancing machine, it is necessary to apply some special structures to its structure on the basis of practice, apply theory in practice, and ultimately ensure that the research and development of its automatic crankshaft balancing machine can provide comprehensive ways and methods for China's dynamic balancing field, ultimately promoting the development of industrial machinery in China.
The specific process of crankshaft dynamic balance correction depends on the number of machining, and the entire process is quite complex. Below is a detailed analysis of the Huake Zhichuang dynamic balance machine. The crankshaft rotates at high speed during operation. If the balance is not good, it will produce momentum peaks, and in severe cases, it can break. Generally, it is tested through a dynamic balancing machine to reduce some materials in the non stressed parts of the crankshaft. All high-speed rotating parts need to undergo balance testing, such as flywheels, transmission shafts, high-speed spindles, etc.
138 browse