The importance of crankshaft dynamic balance and the process characteristics of crankshaft balancing machine
The specific process of crankshaft dynamic balance correction depends on the number of machining, and the entire process is quite complex. Below is a detailed analysis of the Huake Zhichuang dynamic balance machine. The crankshaft rotates at high speed during operation. If the balance is not good, it will produce momentum peaks, and in severe cases, it can break. Generally, it is tested through a dynamic balancing machine to reduce some materials in the non stressed parts of the crankshaft. All high-speed rotating parts need to undergo balance testing, such as flywheels, transmission shafts, high-speed spindles, etc.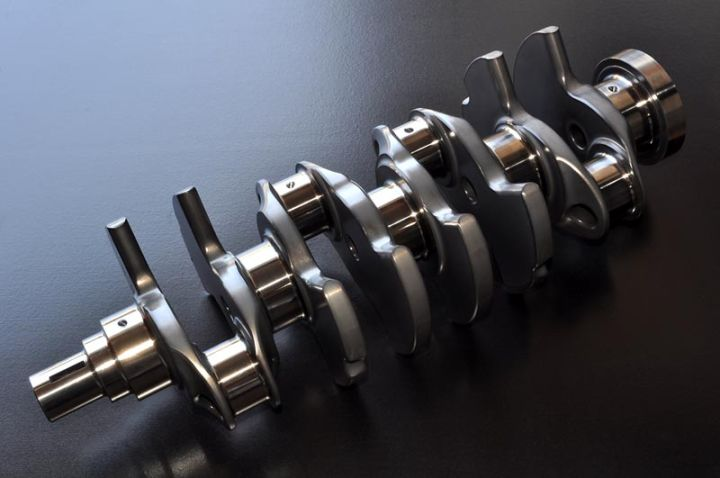
The crankshaft is the main rotating component of the engine. After installing the connecting rod, it can receive the up and down (reciprocating) motion of the connecting rod and transform it into a cyclic (rotating) motion. It is an important component of the engine. Rotation generates vibration, so dynamic balancing is necessary. View crankshaft specific dynamic balancing machine series Click: Ring belt balancing machine, universal joint balancing machine
1、 Manufacturing raw materials
1. If it is a single piece, perhaps produced in small batches, sometimes using bar materials for direct processing. To put it simply, it is to hard cut a casting rod into a crankshaft, which looks like a waste of material but actually reduces the difficulty of casting and can save costs. However, the requirements for processing equipment are relatively high; Perhaps using free forging to shape a bar into a shape similar to a crankshaft, but casting requires a sufficiently large forging machine or press
2. If processing in batches, forging is generally used, and the bar material is directly cast with a mold, resulting in the shape of the crankshaft. This method saves energy, labor, and materials, but making a set of molds is very expensive.
2、 Rough machining
1. Generally, small factories or small-scale enterprises can choose CNC lathes and crankshaft lathes, or simply use regular lathes. The difficulty in machining the crankshaft lies in machining the "crank", which is the connecting rod neck part, which requires clamping the crankshaft when it is misaligned. Adjust the center of the section of "crankshaft" to be processed to be aligned with the spindle center of the lathe, and then process each "crankshaft" one by one. For each machining, the crankshaft needs to be re clamped, which is time-consuming and laborious. As for the main journal of the crankshaft, it is very simple to directly turn it.
2. Professional processing factories generally choose CNC crankshaft milling machines, which can be divided into sub milling and external milling. Internal milling has high precision and fast speed, but it is more expensive and can only process circular surfaces; External milling has low precision and slow speed, but is cheaper than internal milling and can process flat surfaces. At the same time, with the same machine scale, external milling can process larger scales than internal milling. The power of crankshaft milling is very high. Generally, the milling cutter rotates around the crankshaft once (for internal milling, the crankshaft is inside the cutter head), or perhaps the crankshaft rotates once (for external milling), and the crankshaft with such a wide cutter head is finished. A crankshaft milling machine can easily top several CNC lathes and a dozen general lathes.
3、 After rough machining of the crankshaft through heat treatment, the hardness is not sufficient. It needs to be quenched/nitrided to increase hardness, and then tempered to avoid cracking of the crankshaft.
4、 Precision machining heat treatment can cause slight deformation of the crankshaft, and the crankshaft accuracy itself does not meet the requirements, which requires the use of a grinder. Small batches can be processed using general grinding machines with low power, especially when machining "bends", which require one by one processing, just like a lathe. Of course, there are also advanced crankshaft grinders, especially CNC follow-up connecting rod neck grinders, which are also very expensive. The small and medium-sized ones cost 20-30 million yuan, and the large ones cost 40-50 million yuan, with no upper limit (these are all considered as half special machines, all customized)
5、 In fact, the machining of the crankshaft itself is almost done at this point, and then operations such as flaw detection, polishing, and dynamic balancing are carried out.
Operation of crankshaft: In terms of material, non quenched and tempered steel, which is currently an energy-saving, efficient, and environmentally friendly green steel, is used. Non quenched and tempered steel is a new type of steel that was introduced in early 1970s and has been used for less than 40 years. It is based on medium carbon manganese steel by adding vanadium, titanium, and niobium microalloying elements, so that its solid solubility decreases with cooling during heating. The ferrite and pearlite precipitated from the microalloying elements vanadium, titanium, and niobium are in a coherent relationship with the parent phase, strengthening the steel. Non quenched and tempered steel can be used to make balance machine parts without quenching and tempering treatment, shortening the production cycle and saving energy. Some can reduce energy consumption and production costs by 25% to 38%.
Nowadays, there are more and more non quenched and tempered steel forgings used for hot forging in the market. Non quenched and tempered steel crankshafts, connecting rods, camshafts and other internal combustion engine components have gained great operational space in industries such as internal combustion engine crankshafts and automobiles.
The crankshaft, also known as the engine spindle, is produced through multi tool turning and manual grinding processes in the early stages of engine operation. It has received a certain degree of praise and operation in a short period of time. In the 21st century, due to the continuous advancement of equipment quality and processing requirements, low processing accuracy and poor flexibility, it is gradually exiting the historical stage after leading for more than half a century. The advanced equipment of high-speed and efficient composite processing technology is gradually entering the engine scale and automobile balancing machine crankshaft scale, and has a considerable degree of operation in processing and production, which is a necessary trend for the growth of modern technology.
The crankshaft is an important component of the engine, made of carbon structural steel or ductile iron. The main shaft neck is installed on the cylinder block, and the connecting rod neck is connected to the connecting rod big end hole. The small end hole on the connecting rod is connected to the cylinder piston, forming a standardized crank slider mechanism. The lubrication of the bearing between the crankshaft and rocker arm is individually pressure lubrication. The core of the crankshaft is connected to the bearing through a process oil passage. When the engine is running, the oil pump supplies pressure oil for lubrication and cooling. The working process of the engine is the combustion of mixed compressed gas, which promotes the piston and transmits force to the crankshaft through the connecting rod, and the crankshaft converts linear motion into translational motion.
An unbalanced crankshaft generates pressure on its supporting structure and the rotor itself during its rotation, leading to vibration. Therefore, dynamic balance of the crankshaft is essential.
The specific process of crankshaft dynamic balance correction depends on the number of machining, and the entire process is quite complex. Below is a detailed analysis of the Huake Zhichuang dynamic balance machine. The crankshaft rotates at high speed during operation. If the balance is not good, it will produce momentum peaks, and in severe cases, it can break. Generally, it is tested through a dynamic balancing machine to reduce some materials in the non stressed parts of the crankshaft. All high-speed rotating parts need to undergo balance testing, such as flywheels, transmission shafts, high-speed spindles, etc.
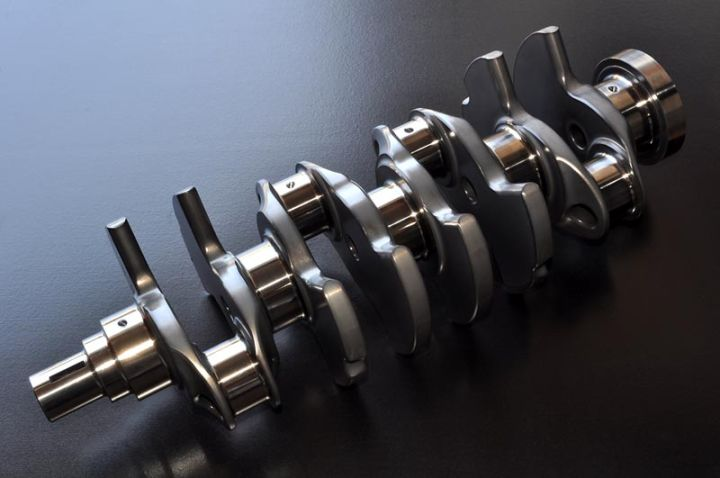
The crankshaft is the main rotating component of the engine. After installing the connecting rod, it can receive the up and down (reciprocating) motion of the connecting rod and transform it into a cyclic (rotating) motion. It is an important component of the engine. Rotation generates vibration, so dynamic balancing is necessary. View crankshaft specific dynamic balancing machine series Click: Ring belt balancing machine, universal joint balancing machine
1、 Manufacturing raw materials
1. If it is a single piece, perhaps produced in small batches, sometimes using bar materials for direct processing. To put it simply, it is to hard cut a casting rod into a crankshaft, which looks like a waste of material but actually reduces the difficulty of casting and can save costs. However, the requirements for processing equipment are relatively high; Perhaps using free forging to shape a bar into a shape similar to a crankshaft, but casting requires a sufficiently large forging machine or press
2. If processing in batches, forging is generally used, and the bar material is directly cast with a mold, resulting in the shape of the crankshaft. This method saves energy, labor, and materials, but making a set of molds is very expensive.
2、 Rough machining
1. Generally, small factories or small-scale enterprises can choose CNC lathes and crankshaft lathes, or simply use regular lathes. The difficulty in machining the crankshaft lies in machining the "crank", which is the connecting rod neck part, which requires clamping the crankshaft when it is misaligned. Adjust the center of the section of "crankshaft" to be processed to be aligned with the spindle center of the lathe, and then process each "crankshaft" one by one. For each machining, the crankshaft needs to be re clamped, which is time-consuming and laborious. As for the main journal of the crankshaft, it is very simple to directly turn it.
2. Professional processing factories generally choose CNC crankshaft milling machines, which can be divided into sub milling and external milling. Internal milling has high precision and fast speed, but it is more expensive and can only process circular surfaces; External milling has low precision and slow speed, but is cheaper than internal milling and can process flat surfaces. At the same time, with the same machine scale, external milling can process larger scales than internal milling. The power of crankshaft milling is very high. Generally, the milling cutter rotates around the crankshaft once (for internal milling, the crankshaft is inside the cutter head), or perhaps the crankshaft rotates once (for external milling), and the crankshaft with such a wide cutter head is finished. A crankshaft milling machine can easily top several CNC lathes and a dozen general lathes.
3、 After rough machining of the crankshaft through heat treatment, the hardness is not sufficient. It needs to be quenched/nitrided to increase hardness, and then tempered to avoid cracking of the crankshaft.
4、 Precision machining heat treatment can cause slight deformation of the crankshaft, and the crankshaft accuracy itself does not meet the requirements, which requires the use of a grinder. Small batches can be processed using general grinding machines with low power, especially when machining "bends", which require one by one processing, just like a lathe. Of course, there are also advanced crankshaft grinders, especially CNC follow-up connecting rod neck grinders, which are also very expensive. The small and medium-sized ones cost 20-30 million yuan, and the large ones cost 40-50 million yuan, with no upper limit (these are all considered as half special machines, all customized)
5、 In fact, the machining of the crankshaft itself is almost done at this point, and then operations such as flaw detection, polishing, and dynamic balancing are carried out.
Operation of crankshaft: In terms of material, non quenched and tempered steel, which is currently an energy-saving, efficient, and environmentally friendly green steel, is used. Non quenched and tempered steel is a new type of steel that was introduced in early 1970s and has been used for less than 40 years. It is based on medium carbon manganese steel by adding vanadium, titanium, and niobium microalloying elements, so that its solid solubility decreases with cooling during heating. The ferrite and pearlite precipitated from the microalloying elements vanadium, titanium, and niobium are in a coherent relationship with the parent phase, strengthening the steel. Non quenched and tempered steel can be used to make balance machine parts without quenching and tempering treatment, shortening the production cycle and saving energy. Some can reduce energy consumption and production costs by 25% to 38%.
Nowadays, there are more and more non quenched and tempered steel forgings used for hot forging in the market. Non quenched and tempered steel crankshafts, connecting rods, camshafts and other internal combustion engine components have gained great operational space in industries such as internal combustion engine crankshafts and automobiles.
The crankshaft, also known as the engine spindle, is produced through multi tool turning and manual grinding processes in the early stages of engine operation. It has received a certain degree of praise and operation in a short period of time. In the 21st century, due to the continuous advancement of equipment quality and processing requirements, low processing accuracy and poor flexibility, it is gradually exiting the historical stage after leading for more than half a century. The advanced equipment of high-speed and efficient composite processing technology is gradually entering the engine scale and automobile balancing machine crankshaft scale, and has a considerable degree of operation in processing and production, which is a necessary trend for the growth of modern technology.
The crankshaft is an important component of the engine, made of carbon structural steel or ductile iron. The main shaft neck is installed on the cylinder block, and the connecting rod neck is connected to the connecting rod big end hole. The small end hole on the connecting rod is connected to the cylinder piston, forming a standardized crank slider mechanism. The lubrication of the bearing between the crankshaft and rocker arm is individually pressure lubrication. The core of the crankshaft is connected to the bearing through a process oil passage. When the engine is running, the oil pump supplies pressure oil for lubrication and cooling. The working process of the engine is the combustion of mixed compressed gas, which promotes the piston and transmits force to the crankshaft through the connecting rod, and the crankshaft converts linear motion into translational motion.
An unbalanced crankshaft generates pressure on its supporting structure and the rotor itself during its rotation, leading to vibration. Therefore, dynamic balance of the crankshaft is essential.
166 browse