Today, we will explain in detail the methods for treating impeller wear and scaling in fan balancing machines. The impeller of the fan impeller balancing machine may become unbalanced if operated improperly during use. The causes of imbalance can be divided into impeller wear, impeller balancing machine imbalance, impeller scaling, etc. The reasons for these situations are directly related to the dust removal device connected to the induced draft fan. Dry dust removal devices can cause impeller imbalance, which can directly lead to impeller wear. Wet dust removal devices can also affect impeller imbalance, which can directly lead to impeller scaling, among which impeller scaling is the most serious problem. After scaling occurs on the impeller, it must be dealt with promptly, otherwise it will have a significant impact on the impeller and even damage the impeller or equipment.
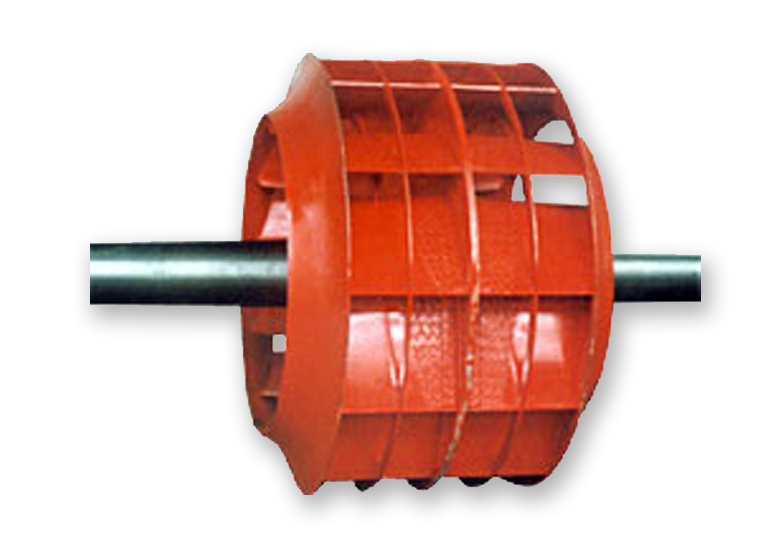
High pressure gas descaling for impeller scaling: This method consists of a nozzle, pipeline, and gas source, and it has a very good descaling effect on the impeller. It can descaling in the gap between the rotation of the impeller balancing machine and can be completed in just a few seconds. The operation is very simple, and multiple descaling operations can be carried out every day, which greatly reduces costs. The pipeline it uses is a high-pressure resistant pipeline, the nozzle is a specialized nozzle, and the gas source is a high-pressure gas source.
Water spray descaling: This method is similar to the high-pressure gas descaling system. The water spray system is installed on the casing of the impeller dynamic balancing machine. It consists of three nozzles, pipes, and drainage holes. The water source is tap water with certain pressure requirements. The effect of this method is good, but the disadvantage is that the descaling time is relatively long each time, and it needs to be shut down multiple times a month for descaling, which will affect the normal use of the impeller dynamic balancing machine. Continuous airflow cleaning: Structurally speaking, the continuous blowing device does not require an external air source. It uses the exhaust pressure of the induced draft fan itself to direct a small amount of flue gas (1% to 2% of the rated air volume) from the inside of the induced draft fan to a dedicated nozzle. The nozzle is located at the inlet of the impeller and sprays the flue gas at a high speed onto the non working surface of the blade. This type of blowing is continuous and starts with the opening of the induced draft fan. It not only blows away the dust that has just adhered to the blade, but also prevents dust deposition and thickening, and does not need to stop the machine for descaling. The device has a simple structure, minimal modifications to the induced draft fan, and excellent anti scaling effect, making it a highly developed new technology.
The above is about the problem of scaling on the impeller of the impeller balancing machine. We hope everyone can refer to it for scaling treatment, and the problem caused by the impeller should be solved according to the actual situation. The descaling method of continuous airflow blowing is very suitable in many factories because it can achieve continuous cleaning effect and solve the problem of dust accumulation on the impeller. Moreover, this method does not require the equipment to be stopped during operation, which can effectively improve work efficiency and reduce consumption costs.
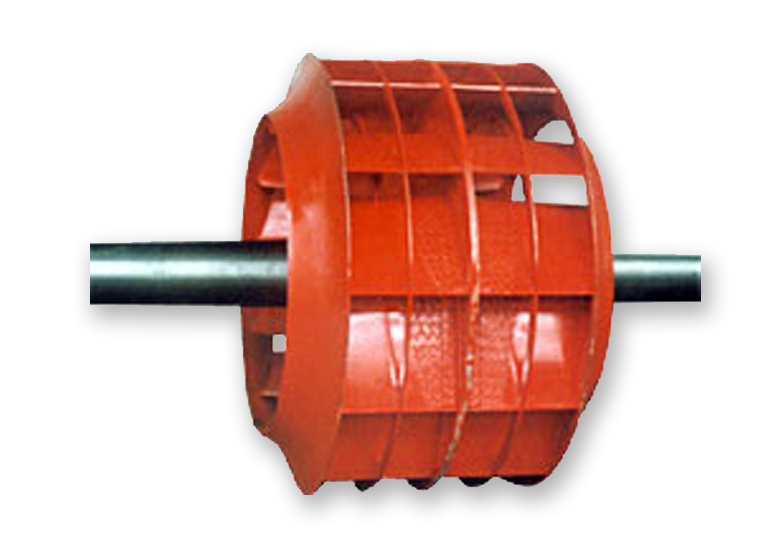
High pressure gas descaling for impeller scaling: This method consists of a nozzle, pipeline, and gas source, and it has a very good descaling effect on the impeller. It can descaling in the gap between the rotation of the impeller balancing machine and can be completed in just a few seconds. The operation is very simple, and multiple descaling operations can be carried out every day, which greatly reduces costs. The pipeline it uses is a high-pressure resistant pipeline, the nozzle is a specialized nozzle, and the gas source is a high-pressure gas source.
Water spray descaling: This method is similar to the high-pressure gas descaling system. The water spray system is installed on the casing of the impeller dynamic balancing machine. It consists of three nozzles, pipes, and drainage holes. The water source is tap water with certain pressure requirements. The effect of this method is good, but the disadvantage is that the descaling time is relatively long each time, and it needs to be shut down multiple times a month for descaling, which will affect the normal use of the impeller dynamic balancing machine. Continuous airflow cleaning: Structurally speaking, the continuous blowing device does not require an external air source. It uses the exhaust pressure of the induced draft fan itself to direct a small amount of flue gas (1% to 2% of the rated air volume) from the inside of the induced draft fan to a dedicated nozzle. The nozzle is located at the inlet of the impeller and sprays the flue gas at a high speed onto the non working surface of the blade. This type of blowing is continuous and starts with the opening of the induced draft fan. It not only blows away the dust that has just adhered to the blade, but also prevents dust deposition and thickening, and does not need to stop the machine for descaling. The device has a simple structure, minimal modifications to the induced draft fan, and excellent anti scaling effect, making it a highly developed new technology.
The above is about the problem of scaling on the impeller of the impeller balancing machine. We hope everyone can refer to it for scaling treatment, and the problem caused by the impeller should be solved according to the actual situation. The descaling method of continuous airflow blowing is very suitable in many factories because it can achieve continuous cleaning effect and solve the problem of dust accumulation on the impeller. Moreover, this method does not require the equipment to be stopped during operation, which can effectively improve work efficiency and reduce consumption costs.
119 browse