At present, there is very little interference in the process of measuring the unbalance of workpieces using a rotor balancing machine, and the detection system has high accuracy and efficiency; It is particularly suitable for dynamic balancing in the production process of rotating mechanical parts and plays an important role in workpiece dynamic balancing. However, there are still a series of issues with the process balancing method.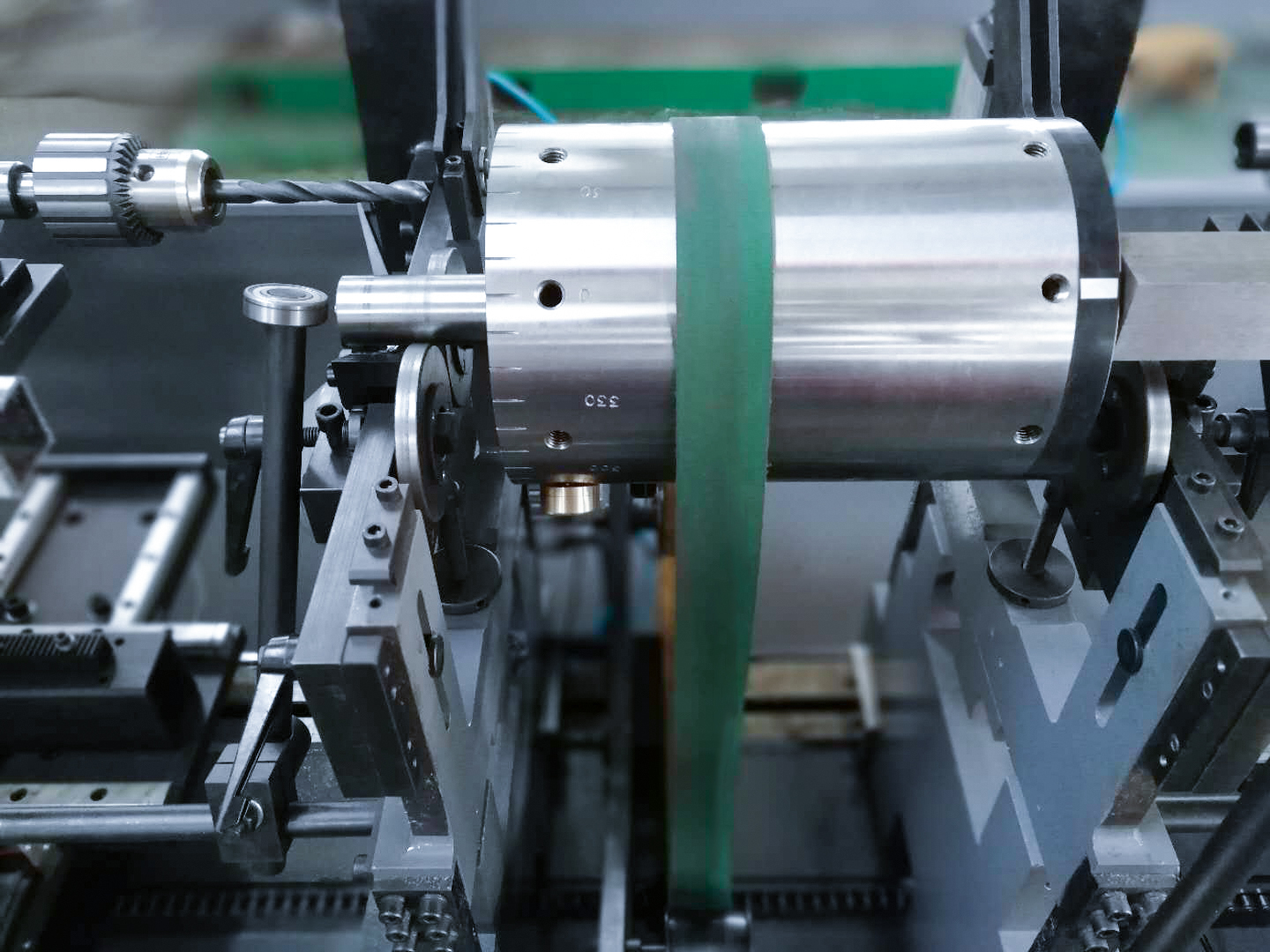
1. Balancing machines, especially high-speed ones, are too expensive.
2. When the rotor is in dynamic balance, the shutdown time is very long and slow, resulting in loss of balance.
3. Due to the limited number of rotors of different sizes and weights, it is difficult (if not impossible) to balance the crane.
For example, high-power steam turbine rotors and large ones without corresponding large balancing devices often result in imbalance; The main frame of a high-temperature steam turbine rotor is usually prone to elastic deformation, and when you stand up, it will automatically disappear. The rotor dynamic balance and thermal balance are obviously unbalanced machines.
4. After installation, dynamically balance the rotor to maintain good balance and ensure accuracy. Due to different support conditions for dynamic balancing rotors, different coordination and balancing rotors, rotor shafts, and equipment are supported. Even after they leave the factory, a high-precision file for dynamic balancing of the balancing rotor is established. The use of transportation and assembly precision balancing work inevitably plays a role, and vibration is not allowed.
In order to overcome the above process balancing method, the technical master of Huake Zhichuang dynamic balancing machine proposed a dynamic balancing method.
The dynamic balancing method described in the assembly operation of a rotating machine is achieved through the use of sensors specifically designed for dynamic balancing machines by Huake Zhichuang. This method processes the information of the vibration generated by the rotor through data processing and accurately determines the position of the rotor unbalance, eliminating the unbalance to a standard state to achieve high-precision dynamic balancing.
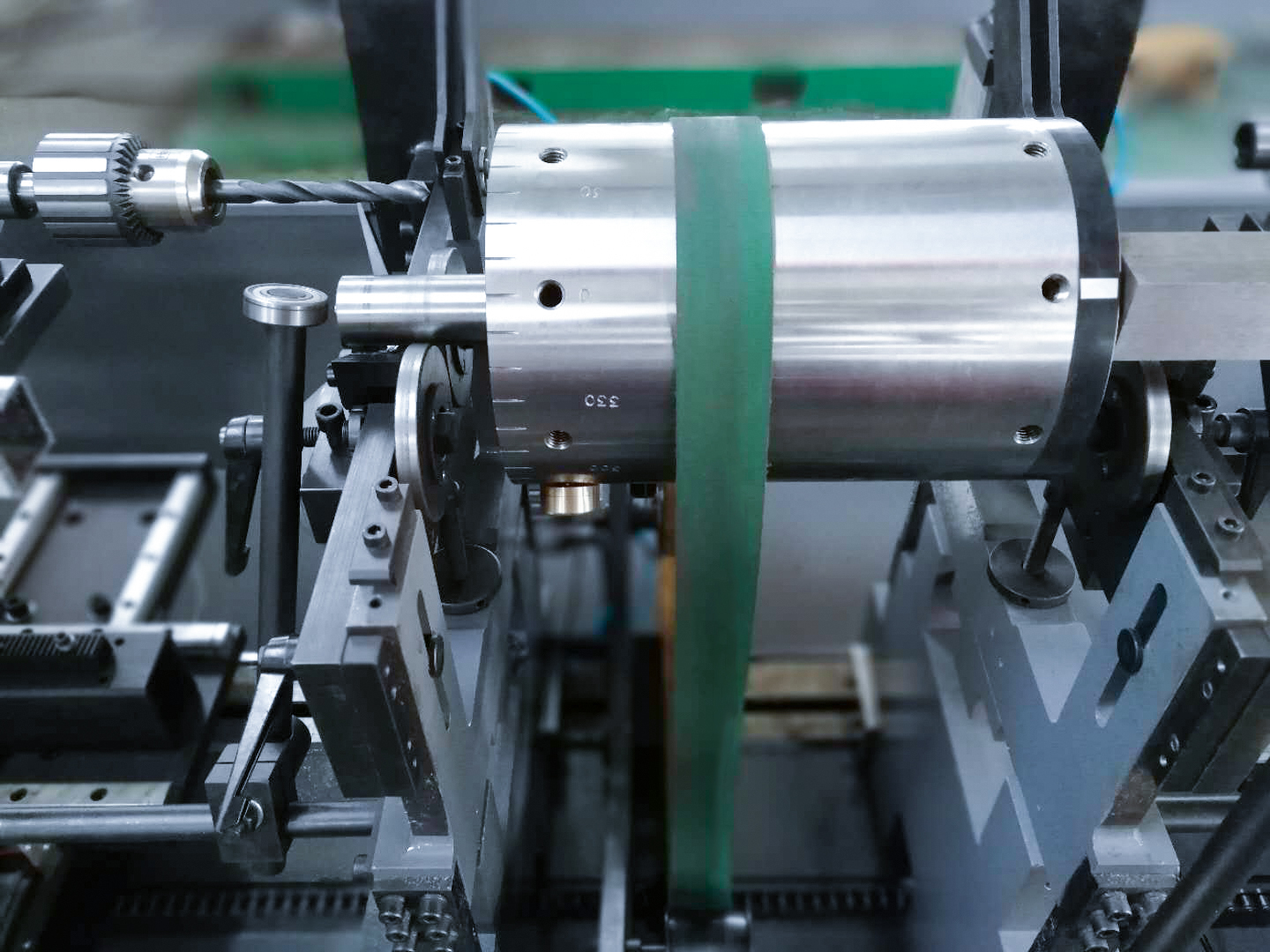
1. Balancing machines, especially high-speed ones, are too expensive.
2. When the rotor is in dynamic balance, the shutdown time is very long and slow, resulting in loss of balance.
3. Due to the limited number of rotors of different sizes and weights, it is difficult (if not impossible) to balance the crane.
For example, high-power steam turbine rotors and large ones without corresponding large balancing devices often result in imbalance; The main frame of a high-temperature steam turbine rotor is usually prone to elastic deformation, and when you stand up, it will automatically disappear. The rotor dynamic balance and thermal balance are obviously unbalanced machines.
4. After installation, dynamically balance the rotor to maintain good balance and ensure accuracy. Due to different support conditions for dynamic balancing rotors, different coordination and balancing rotors, rotor shafts, and equipment are supported. Even after they leave the factory, a high-precision file for dynamic balancing of the balancing rotor is established. The use of transportation and assembly precision balancing work inevitably plays a role, and vibration is not allowed.
In order to overcome the above process balancing method, the technical master of Huake Zhichuang dynamic balancing machine proposed a dynamic balancing method.
The dynamic balancing method described in the assembly operation of a rotating machine is achieved through the use of sensors specifically designed for dynamic balancing machines by Huake Zhichuang. This method processes the information of the vibration generated by the rotor through data processing and accurately determines the position of the rotor unbalance, eliminating the unbalance to a standard state to achieve high-precision dynamic balancing.
100 browse