What are the key reasons for the imbalance caused by the fan impeller? The reasons for the imbalance caused by impellers in application can be briefly divided into two types: impeller wear and impeller scaling. The two situations are related to the ash removal equipment connected before the induced draft fan. The dry ash removal equipment causes the impeller to be unbalanced mainly due to wear, while the wet ash removal equipment harms the impeller imbalance mainly due to scaling. The technical master of the dynamic balancing machine is now described as follows:
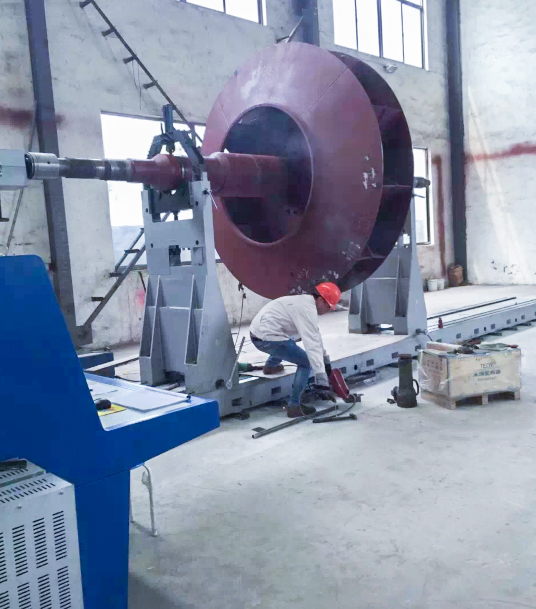
1. Wear of impeller:
Although the dry test ash removal equipment can remove the vast majority of large particles in the smoke and dust, small amounts of large particles and many fine smoke particles accompany the high-temperature and high-speed smoke and dust, causing the blades to be continuously eroded by the induced draft fan. Over time, blade like wear will occur at the inlet and outlet of the blades. Because this type of wear is irregular, it leads to the imbalance of the impeller. In addition, the surface of the impeller is easily oxidized at high temperatures, transforming into a thick oxide layer. The bonding force between this oxide scale and the surface of the impeller is not uniform, and some oxide scales will automatically fall off under the action of vibration or centrifugal force, which is also one of the reasons for the imbalance of the impeller.
2. Scaling of impeller:
The humidity of the smoke and dust purified by the wet ash removal equipment (Venturi water film dust collector) is too high, and the uncleaned smoke and dust particles, although very small, have a high viscosity. When they use induced draft fans, they can be sucked onto the non working surface of the blades under the action of gas vortices, resulting in severe smoke and dust scaling at the inlet and outlet of the non working surface, and gradually thickening. When some of the dust falls off under the combined action of centrifugal force and vibration, the balance of the impeller is destroyed, and the entire induced draft fan is caused to vibrate.
2、 Preventive measures to address impeller imbalance
1. Ways to solve impeller wear:
The best way to prevent impeller damage caused by dry ash removal is to enhance the wear resistance of the impeller, in addition to improving the ash removal function of the dust removal equipment. At present, the more mature method in this regard is thermal spraying technology, which uses a unique way to transform wear-resistant and heat-resistant materials such as metals or ceramics into high-temperature and high-speed particle flows, spray paint onto the surface of the impeller blades, and produce a strong outer layer with much higher wear resistance, heat resistance, and oxidation resistance than the blade material itself. This not only reduces the damage caused by the impeller's dynamic balance, but also mitigates the unevenness caused by the oxide layer.
When using induced draft fans, it is optimal to use impellers that have been thermally sprayed for dry ash removal. For impellers that have not been solved by thermal spraying in applications, thermal spraying treatment can be considered for impellers during equipment maintenance. Although this will increase the production or maintenance costs of the impeller, it will increase the service life of the impeller by 1-2 times and increase the maintenance cycle of the induced draft fan. This further reduces the operating profit of the induced draft fan and the entire manufacturing system, resulting in excellent overall benefits.
2. Ways to handle impeller scaling:
(1) Spray descaling: It is a common descaling method, and the sprinkler system is installed on the casing of the induced draft fan, consisting of pipes, three nozzles (one at the impeller outlet and two at the inlet), and drainage holes. The water source is usually tap water, with a pressure of about 0.3 MPa. This type of approach is generally reasonable. The drawback is that the duration of each shutdown for descaling is relatively long, requiring multiple shutdowns per month for descaling. Endangering the normal operation of the unit.
(2) High pressure gas descaling: This system adopts a structure similar to the sprinkler system, but its pipelines are high-pressure resistant pipelines, dedicated nozzles, and high-pressure gas sources. This type of equipment can quickly and reasonably remove scale from the blades. It can open the high-pressure air source during the normal shutdown of the induced draft fan and successfully remove the scale in just a few tens of seconds. Due to its simple and convenient operation, it can be carried out many times a day, which not only solves the difficult and costly problem of manual descaling, but also sharply reduces the production cost of the entire unit. The question is whether the customer has a pre made high-pressure gas source (with a pressure between 0.8 and 1.5 MPa, which can be compressed air or nitrogen), otherwise a dedicated high-pressure compressor equipment is required.
(3) Continuous airflow for cleaning: Structurally speaking, the continuous blowing equipment does not require an external air source. It uses the exhaust pressure of the induced draft fan itself to direct a small amount of smoke and dust (1% to 2% of the rated wind speed) from the inside of the induced draft fan to a dedicated nozzle located at the inlet of the impeller. At a high speed, the smoke and dust are coughed into the non working surface of the blade. This type of blowing is continuous and starts with the opening of the induced draft fan. It not only blows away the smoke and dust that have just adhered to the blade, but also avoids the deposition and thickening of smoke and dust, and does not need to shut down for cleaning. This device has a simple structure, minimal modification to the induced draft fan, and excellent anti scaling effect, making it a highly developed new technology.
3. Calibration of impeller dynamic balancing machine:
Whether using impellers treated with thermal spraying or impellers cleaned by various methods, their effectiveness is not easy to achieve once and for all. After prolonged use, induced draft fans may still experience vibration exceeding the allowable upper limit. At this point, the problem of impeller imbalance can only be addressed through dynamic balance correction. In the past, the dynamic balance correction of impellers was generally carried out on a dynamic balancing machine, which was very inconvenient for induced draft fans in applications, especially large fans. Therefore, on-site dynamic balancing technology has gained increasing attention in recent years. The key advantages of it compared to the past are
(1) Avoiding tedious dismantling work, saving dismantling and transportation costs, and reducing maintenance time;
(2) Stored the original installation precision and improved the balance precision of all induced draft fan systems. The testing standards are briefly described as follows.
Testing equipment: On site dynamic balancing instrument
Test steps:
(1) Stick reflective strips on the fan shaft and measure the original vibration values: direct frequency amplitude Vrmso, power frequency amplitude Vo, phase angle φ o;
(2) Measure the vibration values after adding the test weight: direct frequency amplitude Vrmsl, power frequency amplitude V1, phase angle φ 1, and automatically calculate the dynamic balance solution results (weight value and angle of adding weight);
(3) After adding the counterweight, measure the remaining vibration values: direct frequency amplitude Vrms2, power frequency amplitude V2, phase angle φ 2. If they can meet the vibration detection standards, it is sufficient.
Testing duration: For skilled on-site testing engineers, completing the above work only takes 1-2 hours. On site dynamic balancing technology is a mature and easy-to-use maintenance technique that can easily, conveniently, and economically resolve unbalanced problems.
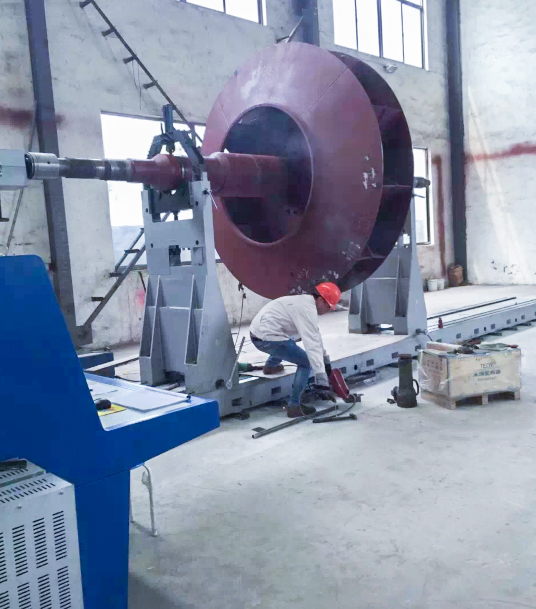
1. Wear of impeller:
Although the dry test ash removal equipment can remove the vast majority of large particles in the smoke and dust, small amounts of large particles and many fine smoke particles accompany the high-temperature and high-speed smoke and dust, causing the blades to be continuously eroded by the induced draft fan. Over time, blade like wear will occur at the inlet and outlet of the blades. Because this type of wear is irregular, it leads to the imbalance of the impeller. In addition, the surface of the impeller is easily oxidized at high temperatures, transforming into a thick oxide layer. The bonding force between this oxide scale and the surface of the impeller is not uniform, and some oxide scales will automatically fall off under the action of vibration or centrifugal force, which is also one of the reasons for the imbalance of the impeller.
2. Scaling of impeller:
The humidity of the smoke and dust purified by the wet ash removal equipment (Venturi water film dust collector) is too high, and the uncleaned smoke and dust particles, although very small, have a high viscosity. When they use induced draft fans, they can be sucked onto the non working surface of the blades under the action of gas vortices, resulting in severe smoke and dust scaling at the inlet and outlet of the non working surface, and gradually thickening. When some of the dust falls off under the combined action of centrifugal force and vibration, the balance of the impeller is destroyed, and the entire induced draft fan is caused to vibrate.
2、 Preventive measures to address impeller imbalance
1. Ways to solve impeller wear:
The best way to prevent impeller damage caused by dry ash removal is to enhance the wear resistance of the impeller, in addition to improving the ash removal function of the dust removal equipment. At present, the more mature method in this regard is thermal spraying technology, which uses a unique way to transform wear-resistant and heat-resistant materials such as metals or ceramics into high-temperature and high-speed particle flows, spray paint onto the surface of the impeller blades, and produce a strong outer layer with much higher wear resistance, heat resistance, and oxidation resistance than the blade material itself. This not only reduces the damage caused by the impeller's dynamic balance, but also mitigates the unevenness caused by the oxide layer.
When using induced draft fans, it is optimal to use impellers that have been thermally sprayed for dry ash removal. For impellers that have not been solved by thermal spraying in applications, thermal spraying treatment can be considered for impellers during equipment maintenance. Although this will increase the production or maintenance costs of the impeller, it will increase the service life of the impeller by 1-2 times and increase the maintenance cycle of the induced draft fan. This further reduces the operating profit of the induced draft fan and the entire manufacturing system, resulting in excellent overall benefits.
2. Ways to handle impeller scaling:
(1) Spray descaling: It is a common descaling method, and the sprinkler system is installed on the casing of the induced draft fan, consisting of pipes, three nozzles (one at the impeller outlet and two at the inlet), and drainage holes. The water source is usually tap water, with a pressure of about 0.3 MPa. This type of approach is generally reasonable. The drawback is that the duration of each shutdown for descaling is relatively long, requiring multiple shutdowns per month for descaling. Endangering the normal operation of the unit.
(2) High pressure gas descaling: This system adopts a structure similar to the sprinkler system, but its pipelines are high-pressure resistant pipelines, dedicated nozzles, and high-pressure gas sources. This type of equipment can quickly and reasonably remove scale from the blades. It can open the high-pressure air source during the normal shutdown of the induced draft fan and successfully remove the scale in just a few tens of seconds. Due to its simple and convenient operation, it can be carried out many times a day, which not only solves the difficult and costly problem of manual descaling, but also sharply reduces the production cost of the entire unit. The question is whether the customer has a pre made high-pressure gas source (with a pressure between 0.8 and 1.5 MPa, which can be compressed air or nitrogen), otherwise a dedicated high-pressure compressor equipment is required.
(3) Continuous airflow for cleaning: Structurally speaking, the continuous blowing equipment does not require an external air source. It uses the exhaust pressure of the induced draft fan itself to direct a small amount of smoke and dust (1% to 2% of the rated wind speed) from the inside of the induced draft fan to a dedicated nozzle located at the inlet of the impeller. At a high speed, the smoke and dust are coughed into the non working surface of the blade. This type of blowing is continuous and starts with the opening of the induced draft fan. It not only blows away the smoke and dust that have just adhered to the blade, but also avoids the deposition and thickening of smoke and dust, and does not need to shut down for cleaning. This device has a simple structure, minimal modification to the induced draft fan, and excellent anti scaling effect, making it a highly developed new technology.
3. Calibration of impeller dynamic balancing machine:
Whether using impellers treated with thermal spraying or impellers cleaned by various methods, their effectiveness is not easy to achieve once and for all. After prolonged use, induced draft fans may still experience vibration exceeding the allowable upper limit. At this point, the problem of impeller imbalance can only be addressed through dynamic balance correction. In the past, the dynamic balance correction of impellers was generally carried out on a dynamic balancing machine, which was very inconvenient for induced draft fans in applications, especially large fans. Therefore, on-site dynamic balancing technology has gained increasing attention in recent years. The key advantages of it compared to the past are
(1) Avoiding tedious dismantling work, saving dismantling and transportation costs, and reducing maintenance time;
(2) Stored the original installation precision and improved the balance precision of all induced draft fan systems. The testing standards are briefly described as follows.
Testing equipment: On site dynamic balancing instrument
Test steps:
(1) Stick reflective strips on the fan shaft and measure the original vibration values: direct frequency amplitude Vrmso, power frequency amplitude Vo, phase angle φ o;
(2) Measure the vibration values after adding the test weight: direct frequency amplitude Vrmsl, power frequency amplitude V1, phase angle φ 1, and automatically calculate the dynamic balance solution results (weight value and angle of adding weight);
(3) After adding the counterweight, measure the remaining vibration values: direct frequency amplitude Vrms2, power frequency amplitude V2, phase angle φ 2. If they can meet the vibration detection standards, it is sufficient.
Testing duration: For skilled on-site testing engineers, completing the above work only takes 1-2 hours. On site dynamic balancing technology is a mature and easy-to-use maintenance technique that can easily, conveniently, and economically resolve unbalanced problems.
72 browse