The on-site dynamic balancing of steam turbine generator units is the main method to solve the vibration problem of the unit. On the one hand, 70% of the vibration problem of the unit is caused by imbalance, and on the other hand, on-site dynamic balancing is relatively simple and feasible compared to other methods for handling vibration. The on-site dynamic balancing of steam turbine generator units belongs to the dynamic balancing of flexible rotor shaft systems, which is more labor-intensive and time-consuming than general on-site dynamic balancing. Therefore, the accuracy of on-site dynamic balancing is required to be high. To solve the problem of unbalanced vibration of the turbine generator shaft system with the minimum number of times, it is necessary to have rich experience in on-site dynamic balancing of the unit shaft system.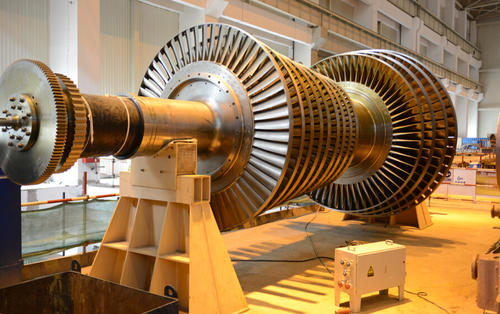
The safety and stability of the equipment components we use mainly depend on the presence of vibration, which is mainly caused by the imbalance of the shaft system. Today, we need to understand the on-site high-speed dynamic balancing machine of the steam turbine generator set, which is the most effective solution for the vibration of the unit.
We can operate based on the vibration theory of flexible rotors. During on-site dynamic balancing of rotors, a very important task before dynamic balancing is to determine whether the vibration mode of the imbalance on the rotor is first order, second order, or third order. The generator rotor operating at the second critical speed will experience deformation of the second order vibration mode of the main span rotor due to the imbalance of the extended end, resulting in vibration characteristics similar to the third order imbalance of the main span rotor. Practice has shown that compared to other forms of vibration, reducing in-phase vibration is sometimes more difficult. We can use the Bode plot for modal analysis of the rotor to determine whether the imbalance is in the same direction or in the opposite direction, whether within or outside the span, and we can use the weighting method to solve it.
Developing a weighting plan for dynamic balancing is the most crucial step. Based on the obtained raw data, there may be multiple weighting plans for on-site dynamic balancing, and we must choose carefully. Firstly, we should first determine the number of times to increase the load. Secondly, in order to achieve the minimum residual vibration, we need to have a great deal of confidence in the weighting process and measurement results, and to minimize the risk in order to implement the correct plan.
Operating steps for on-site dynamic balancing machine of steam turbine generator set:
1. Develop an implementable weighting plan for the dynamic balancing machine and determine the weighting operation steps.
2. Attempting to weigh and obtain weight data is not a necessary step.
3. Measure the vibration data, analyze and record it.
4. Formal aggravation.
On site dynamic balancing has a history of decades in the power industry, and it can be said that it was initiated in the power industry. There are many people studying dynamic balance in this industry, and many experts have conducted extensive theoretical research and accumulated rich experience in shaft system dynamic balance time.
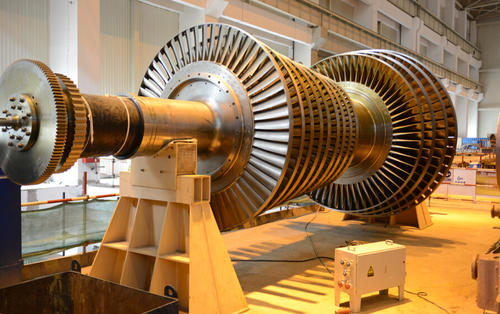
The safety and stability of the equipment components we use mainly depend on the presence of vibration, which is mainly caused by the imbalance of the shaft system. Today, we need to understand the on-site high-speed dynamic balancing machine of the steam turbine generator set, which is the most effective solution for the vibration of the unit.
We can operate based on the vibration theory of flexible rotors. During on-site dynamic balancing of rotors, a very important task before dynamic balancing is to determine whether the vibration mode of the imbalance on the rotor is first order, second order, or third order. The generator rotor operating at the second critical speed will experience deformation of the second order vibration mode of the main span rotor due to the imbalance of the extended end, resulting in vibration characteristics similar to the third order imbalance of the main span rotor. Practice has shown that compared to other forms of vibration, reducing in-phase vibration is sometimes more difficult. We can use the Bode plot for modal analysis of the rotor to determine whether the imbalance is in the same direction or in the opposite direction, whether within or outside the span, and we can use the weighting method to solve it.
Developing a weighting plan for dynamic balancing is the most crucial step. Based on the obtained raw data, there may be multiple weighting plans for on-site dynamic balancing, and we must choose carefully. Firstly, we should first determine the number of times to increase the load. Secondly, in order to achieve the minimum residual vibration, we need to have a great deal of confidence in the weighting process and measurement results, and to minimize the risk in order to implement the correct plan.
Operating steps for on-site dynamic balancing machine of steam turbine generator set:
1. Develop an implementable weighting plan for the dynamic balancing machine and determine the weighting operation steps.
2. Attempting to weigh and obtain weight data is not a necessary step.
3. Measure the vibration data, analyze and record it.
4. Formal aggravation.
On site dynamic balancing has a history of decades in the power industry, and it can be said that it was initiated in the power industry. There are many people studying dynamic balance in this industry, and many experts have conducted extensive theoretical research and accumulated rich experience in shaft system dynamic balance time.
195 browse