Brushless motors are mainly composed of two parts: an electric motor and a driver. Brushless motors belong to electromechanical integrated equipment. The development of brushless motors in China has a short history. With the rapid development of science and technology in China, brushless motors have been applied in many fields, such as household appliances, toys, models, electric vehicles, and so on. Using too much can also lead to various problems, one of which is the balance problem. Let's learn together how to choose a dynamic balancing machine for brushless motors.
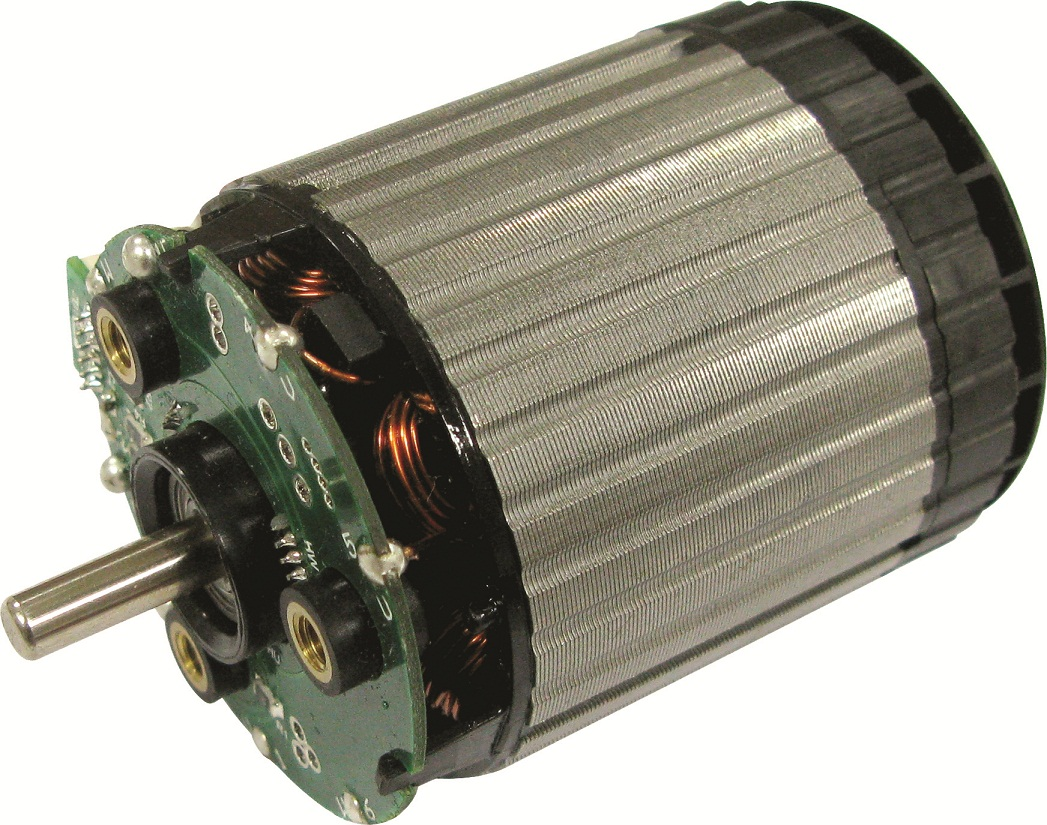
Brushless motor dynamic balance detection
The centrifugal force generated by the uneven distribution of mass relative to the axis during the rotation of any rotor around its axis, which acts on the bearings of the rotor and causes vibration, noise, and accelerated bearing wear, seriously affecting the performance and service life of the product. In order to control the vibration, noise, and service life of brushless motors, it is necessary to achieve a high level of rotor dynamic balance accuracy. Choosing the brushless motor fully automatic balancing machine developed by Shenman can effectively solve the dynamic balancing problem of the rotor and improve production efficiency.
Brushless motor dynamic balance correction
When choosing a dynamic balancing machine, we should not only focus on the type of balancing machine, nor blindly follow others or online comments to choose the model of balancing machine. Everything should be explored by ourselves, and the answers we get are the best basis for judging the quality of the type.
The first thing to consider for a brushless motor is whether to use a vertical dynamic balancing machine or a horizontal dynamic balancing machine. However, there is no definite answer or explanation for this. Because as long as any type of dynamic balancing machine model can achieve high-precision and stable detection, then any type of dynamic balancing machine is acceptable. The purpose of testing is to see if the final result can meet the user's requirements.
In addition, the accuracy and stability of the dynamic balancing machine detection are also the criteria for judgment. As long as a vertical or horizontal dynamic balancing machine is selected, regardless of which model can meet this requirement, it can be selected. Some balancing machines have incorporated the calibration device as part of the balancing machine. Gravity balancing machines and centrifugal balancing machines are two typical types of balancing machines, and gravity balancing machines are generally referred to as static balancing machines.
Motor rotor dynamic balancing machine
Therefore, a balancing machine is an essential equipment for reducing vibration, improving performance, and enhancing quality. Usually, the balance of a rotor includes two steps: measuring and correcting the imbalance. The balance machine is mainly used for measuring the imbalance, and the correction of the imbalance is often completed with the help of other auxiliary equipment such as drilling machines, milling machines, and spot welding machines, or by manual methods.
During the manufacturing process, rotating components such as motor rotors, machine tool spindles, internal combustion engine crankshafts and turbine rotors, gyroscopic rotors, and clock pendulums need to be balanced in order to operate smoothly and normally. The correction of rotor unbalance based on the data measured by the balancing machine can improve the distribution of rotor mass relative to the axis, reducing the vibration generated during rotor rotation or the vibration force acting on bearings to the allowable range.
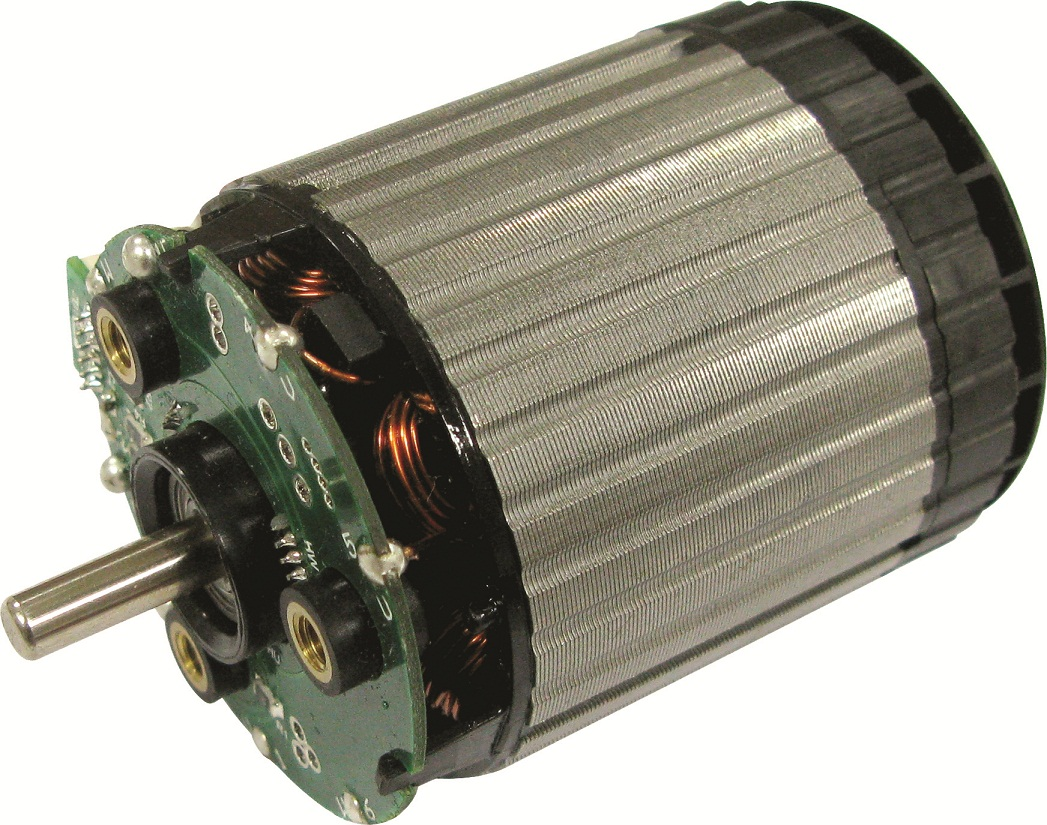
Brushless motor dynamic balance detection
The centrifugal force generated by the uneven distribution of mass relative to the axis during the rotation of any rotor around its axis, which acts on the bearings of the rotor and causes vibration, noise, and accelerated bearing wear, seriously affecting the performance and service life of the product. In order to control the vibration, noise, and service life of brushless motors, it is necessary to achieve a high level of rotor dynamic balance accuracy. Choosing the brushless motor fully automatic balancing machine developed by Shenman can effectively solve the dynamic balancing problem of the rotor and improve production efficiency.
Brushless motor dynamic balance correction
When choosing a dynamic balancing machine, we should not only focus on the type of balancing machine, nor blindly follow others or online comments to choose the model of balancing machine. Everything should be explored by ourselves, and the answers we get are the best basis for judging the quality of the type.
The first thing to consider for a brushless motor is whether to use a vertical dynamic balancing machine or a horizontal dynamic balancing machine. However, there is no definite answer or explanation for this. Because as long as any type of dynamic balancing machine model can achieve high-precision and stable detection, then any type of dynamic balancing machine is acceptable. The purpose of testing is to see if the final result can meet the user's requirements.
In addition, the accuracy and stability of the dynamic balancing machine detection are also the criteria for judgment. As long as a vertical or horizontal dynamic balancing machine is selected, regardless of which model can meet this requirement, it can be selected. Some balancing machines have incorporated the calibration device as part of the balancing machine. Gravity balancing machines and centrifugal balancing machines are two typical types of balancing machines, and gravity balancing machines are generally referred to as static balancing machines.
Motor rotor dynamic balancing machine
Therefore, a balancing machine is an essential equipment for reducing vibration, improving performance, and enhancing quality. Usually, the balance of a rotor includes two steps: measuring and correcting the imbalance. The balance machine is mainly used for measuring the imbalance, and the correction of the imbalance is often completed with the help of other auxiliary equipment such as drilling machines, milling machines, and spot welding machines, or by manual methods.
During the manufacturing process, rotating components such as motor rotors, machine tool spindles, internal combustion engine crankshafts and turbine rotors, gyroscopic rotors, and clock pendulums need to be balanced in order to operate smoothly and normally. The correction of rotor unbalance based on the data measured by the balancing machine can improve the distribution of rotor mass relative to the axis, reducing the vibration generated during rotor rotation or the vibration force acting on bearings to the allowable range.
143 browse