When the mechanical rotor is in operation, the unbalanced inertia force generated by the components will cause additional dynamic pressure in the motion pair; This not only increases friction in the motion range and internal stress in the components, but also reduces mechanical efficiency and service life; Moreover, since the magnitude and direction of these inertial forces are generally periodic, they will inevitably cause forced vibrations in the machinery and its foundation. If its amplitude is large or its frequency is close to the mechanical resonance frequency, it will cause extremely adverse consequences. Not only will it affect the normal operation and service life of the machinery itself, but it will also affect or even damage nearby factory machinery and building structures.
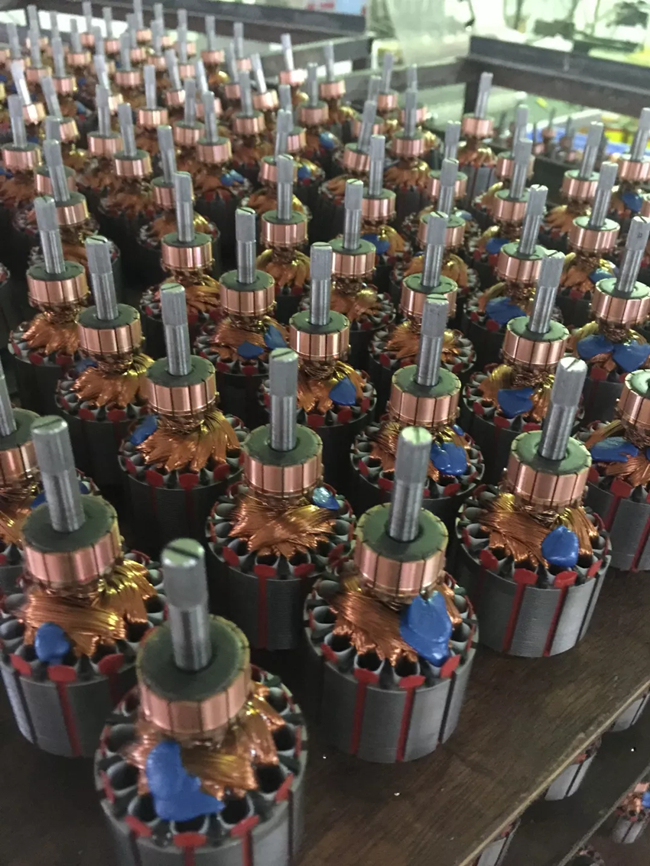
1. The purpose of mechanical rotor dynamic balance correction is to generate additional dynamic pressure in the motion pair due to the unbalanced inertia force generated by the components during the operation of the machinery. This not only increases the friction in the motion range and internal stress in the components, reduces mechanical efficiency and service life, but also causes forced vibration of the machinery and its foundation because the magnitude and direction of these inertial forces are generally periodic. If its amplitude is large or its frequency is close to the mechanical resonance frequency, it will cause extremely adverse consequences. Not only will it affect the normal operation and service life of the machinery itself, but it will also affect or even damage nearby factory machinery and building structures.
The purpose of mechanical rotor dynamic balance correction is to find ways to balance the unbalanced inertia force of components to eliminate or reduce the adverse effects of inertia force. However, it should be pointed out that some machinery works by utilizing the vibration caused by the unbalanced inertia force generated by components, such as vibration compactors, massage machines, vibration pile drivers, vibration conveyors, etc.
2. The content of mechanical rotor dynamic balance: In machinery, due to the different structures and motion forms of each component, the inertia force generated and the balance method are also different. Based on this, mechanical balance problems can be divided into the following two categories.
3. Inertial force balance of components rotating around a fixed axis:
(1) Balance of rigid rotors: In general machinery, the rigidity of the rotor is relatively good, the resonance speed is high, and the working speed of the rotor is lower than (0.6-0.75) (the first resonance speed of the rotor). At this point, the elastic deformation generated by the rotor is very small. This type of rotor is called a rigid rotor. If only its inertial force balance is required, it is called the static balance of the rotor; If the balance of inertia force and inertia moment is required simultaneously, it is called the dynamic balance of the rotor.
(2) Balancing of flexible rotors: Balancing rotors with operating speeds greater than the first critical speed. Some machinery, such as turbine engines, have a large mass and span, but smaller radial dimensions. Therefore, its resonance speed is low. If the working speed is greater than (0.6~0.75), the rotor undergoes significant deformation during operation, resulting in a significant increase in inertial force. This type of rotor is called a flexible rotor.
3. Institutional balance: generally refers to the balance of mechanisms with reciprocating or planar composite motion components. Inertial forces and moments cannot be eliminated inside the components. All inertial forces and moments on the components can be combined into a total inertial force and moment that passes through the center of mass of the mechanism and acts on the frame.
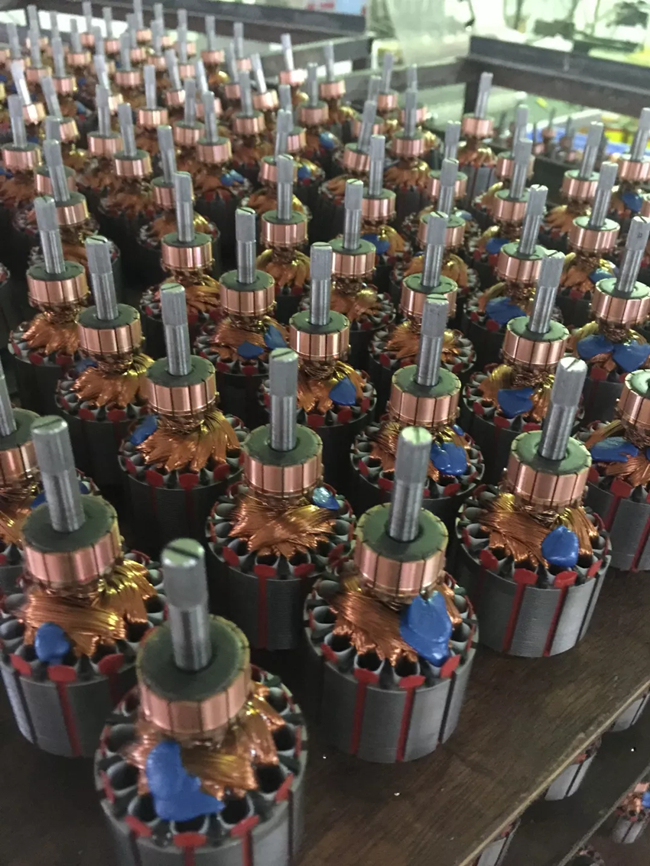
1. The purpose of mechanical rotor dynamic balance correction is to generate additional dynamic pressure in the motion pair due to the unbalanced inertia force generated by the components during the operation of the machinery. This not only increases the friction in the motion range and internal stress in the components, reduces mechanical efficiency and service life, but also causes forced vibration of the machinery and its foundation because the magnitude and direction of these inertial forces are generally periodic. If its amplitude is large or its frequency is close to the mechanical resonance frequency, it will cause extremely adverse consequences. Not only will it affect the normal operation and service life of the machinery itself, but it will also affect or even damage nearby factory machinery and building structures.
The purpose of mechanical rotor dynamic balance correction is to find ways to balance the unbalanced inertia force of components to eliminate or reduce the adverse effects of inertia force. However, it should be pointed out that some machinery works by utilizing the vibration caused by the unbalanced inertia force generated by components, such as vibration compactors, massage machines, vibration pile drivers, vibration conveyors, etc.
2. The content of mechanical rotor dynamic balance: In machinery, due to the different structures and motion forms of each component, the inertia force generated and the balance method are also different. Based on this, mechanical balance problems can be divided into the following two categories.
3. Inertial force balance of components rotating around a fixed axis:
(1) Balance of rigid rotors: In general machinery, the rigidity of the rotor is relatively good, the resonance speed is high, and the working speed of the rotor is lower than (0.6-0.75) (the first resonance speed of the rotor). At this point, the elastic deformation generated by the rotor is very small. This type of rotor is called a rigid rotor. If only its inertial force balance is required, it is called the static balance of the rotor; If the balance of inertia force and inertia moment is required simultaneously, it is called the dynamic balance of the rotor.
(2) Balancing of flexible rotors: Balancing rotors with operating speeds greater than the first critical speed. Some machinery, such as turbine engines, have a large mass and span, but smaller radial dimensions. Therefore, its resonance speed is low. If the working speed is greater than (0.6~0.75), the rotor undergoes significant deformation during operation, resulting in a significant increase in inertial force. This type of rotor is called a flexible rotor.
3. Institutional balance: generally refers to the balance of mechanisms with reciprocating or planar composite motion components. Inertial forces and moments cannot be eliminated inside the components. All inertial forces and moments on the components can be combined into a total inertial force and moment that passes through the center of mass of the mechanism and acts on the frame.
127 browse