What are the technical characteristics of on-site dynamic balancing instruments?
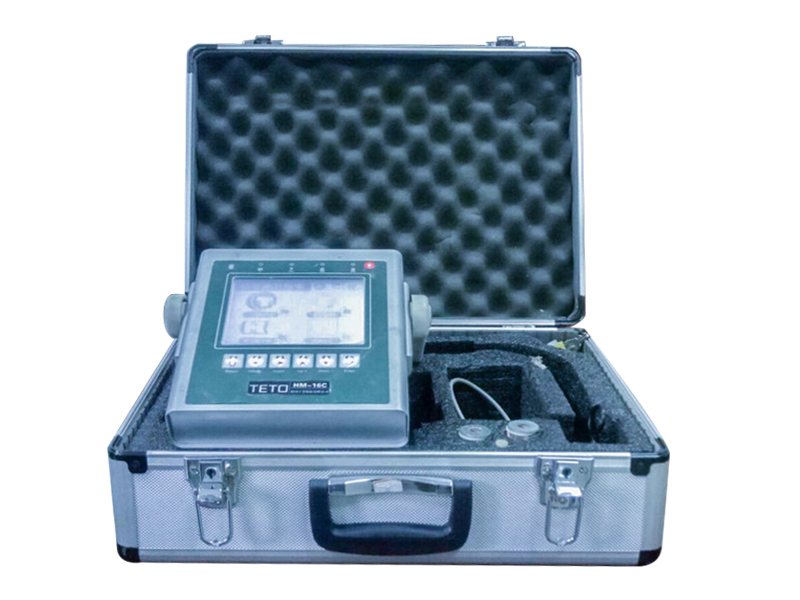
For rotating equipment, good balance correction can extend the lifespan of its components by several times, even tens or hundreds of times. The definition of on-site online dynamic balance correction provided by KM is to directly implement on-site dynamic balance correction without disassembling rotating parts such as impellers and rotors.
The main function of the on-site dynamic balancing instrument is to be convenient and fast, without the need to disassemble the equipment. Determine whether there is a dynamic balance problem by detecting the vibration level. Then repair the equipment according to the system prompts. Thus solving the problem of dynamic balance. The main functions of a dynamic balancing instrument are vibration measurement, spectrum analysis, data acquisition, and on-site dynamic balancing.
Application scope of on-site dynamic balancing instrument: rotating components such as fan impellers, pump impellers, shafts, drums, motor rotors, and machining machine spindles.
The advantages of implementing on-site dynamic balance correction are:
1. There is no need to disassemble the rotating parts, reducing downtime. On site online balance calibration generally only takes about an hour.
2. Calibration can be carried out at actual working speeds. Usually, when the rotating parts are disassembled and calibrated under the balancing machine, calibration cannot be carried out at high speeds. However, on-site online dynamic balancing calibration can calibrate high speeds up to 60000 revolutions per minute.
3. There are many factors that affect balance, including the balance of all rotating components (impeller, shaft, coupling, key seat, etc.) and factors such as installation clearance and deviation angle of rotating parts. Therefore, direct online balancing can achieve better balance effect.
4. The problem of vibration in rotating equipment is sometimes unrelated to balance, and the use of on-site dynamic balancing instruments can immediately detect whether there is a problem of poor balance, avoiding unnecessary balance correction.
5. Double sided dynamic balance correction is different from single plane correction. When the ratio of the diameter to width of the rotating part is less than twice, double plane correction may be required.
The on-site balancing instrument is mainly used for measuring the dynamic balance of rotating machinery such as steam turbines, water turbines, agricultural machines, centrifuges, fans, and water pumps on site, correcting dynamic balance, and analyzing signals. A portable on-site dynamic balancing instrument is launched by integrating advanced embedded computer technology and proven dynamic balancing technology.
It has many functions such as on-site vibration data measurement, vibration analysis, and single and double-sided dynamic balancing. It is simple and easy to use, and is an ideal tool for predictive maintenance and repair in industrial and mining enterprises, especially for equipment manufacturers such as fans and motors and vibration technology service agencies. It can not only perform dynamic balancing of equipment on site, but also perform vibration detection and analysis.
A balancing machine is a device that can measure the imbalance of the equipment rotor. By performing balancing correction on the equipment rotor, the service life of the rotor and equipment can be extended several times, even tens or hundreds of times. Therefore, dynamic balancing of the rotor is very important. A balancing machine can achieve the allowable balance accuracy level of the rotor and also reduce the mechanical vibration amplitude generated by the rotor within the allowable range.
On site dynamic balancing instrument calibration is essential in current industrial use, and the technology of on-site balancing calibration has been widely applied in modern industry. Because the characteristics of on-site dynamic balance correction technology are very advantageous for many manufacturers. Fully understanding the characteristics of on-site dynamic balancing machine calibration technology enables us to better choose and use it.
Technical characteristics of on-site dynamic balancing instrument:
1. The on-site dynamic balancing instrument can achieve the effect of dynamic balancing without disassembling the rotor, which can effectively save downtime, manpower, and material resources. The entire process of on-site dynamic balancing calibration usually only takes about an hour to complete.
2. There are two types of on-site dynamic balancing instruments: double-sided dynamic balancing calibration and single-sided dynamic balancing calibration. However, double-sided dynamic balancing calibration is different from single-sided dynamic balancing calibration. When the diameter to width ratio of the rotor is less than twice, the double-sided dynamic balancing calibration method should be selected.
3. The rotor balance calibration can be implemented based on the actual working speed of the workpiece. When we disassemble the workpiece and calibrate it on the balancing machine, we cannot calibrate it in the high-speed gear. However, the on-site dynamic balancing instrument calibration can achieve high-speed rotation with a calibration speed of up to 60000 revolutions per minute.
4. Sometimes the vibration problem caused by the rotor may not be related to the rotor imbalance, so we can use an on-site dynamic balancing instrument to determine whether the vibration caused by the rotor is related to balance, which can avoid unnecessary balance correction.
5. In fact, there are many other factors that can affect rotor imbalance, such as clearances and angular deviations during rotor installation, which can also affect rotor imbalance. So we choose on-site dynamic balance correction to achieve a balanced state of the rotor, reducing vibration and damage to the equipment.
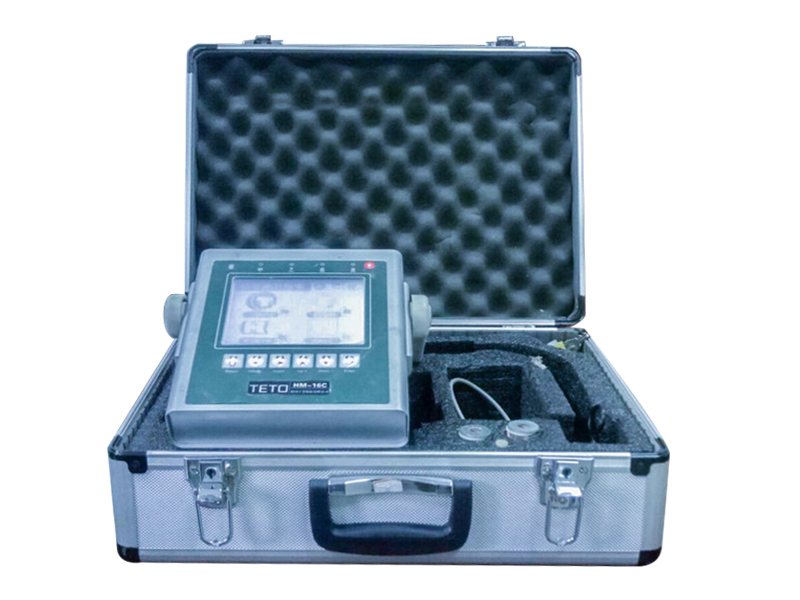
For rotating equipment, good balance correction can extend the lifespan of its components by several times, even tens or hundreds of times. The definition of on-site online dynamic balance correction provided by KM is to directly implement on-site dynamic balance correction without disassembling rotating parts such as impellers and rotors.
The main function of the on-site dynamic balancing instrument is to be convenient and fast, without the need to disassemble the equipment. Determine whether there is a dynamic balance problem by detecting the vibration level. Then repair the equipment according to the system prompts. Thus solving the problem of dynamic balance. The main functions of a dynamic balancing instrument are vibration measurement, spectrum analysis, data acquisition, and on-site dynamic balancing.
Application scope of on-site dynamic balancing instrument: rotating components such as fan impellers, pump impellers, shafts, drums, motor rotors, and machining machine spindles.
The advantages of implementing on-site dynamic balance correction are:
1. There is no need to disassemble the rotating parts, reducing downtime. On site online balance calibration generally only takes about an hour.
2. Calibration can be carried out at actual working speeds. Usually, when the rotating parts are disassembled and calibrated under the balancing machine, calibration cannot be carried out at high speeds. However, on-site online dynamic balancing calibration can calibrate high speeds up to 60000 revolutions per minute.
3. There are many factors that affect balance, including the balance of all rotating components (impeller, shaft, coupling, key seat, etc.) and factors such as installation clearance and deviation angle of rotating parts. Therefore, direct online balancing can achieve better balance effect.
4. The problem of vibration in rotating equipment is sometimes unrelated to balance, and the use of on-site dynamic balancing instruments can immediately detect whether there is a problem of poor balance, avoiding unnecessary balance correction.
5. Double sided dynamic balance correction is different from single plane correction. When the ratio of the diameter to width of the rotating part is less than twice, double plane correction may be required.
The on-site balancing instrument is mainly used for measuring the dynamic balance of rotating machinery such as steam turbines, water turbines, agricultural machines, centrifuges, fans, and water pumps on site, correcting dynamic balance, and analyzing signals. A portable on-site dynamic balancing instrument is launched by integrating advanced embedded computer technology and proven dynamic balancing technology.
It has many functions such as on-site vibration data measurement, vibration analysis, and single and double-sided dynamic balancing. It is simple and easy to use, and is an ideal tool for predictive maintenance and repair in industrial and mining enterprises, especially for equipment manufacturers such as fans and motors and vibration technology service agencies. It can not only perform dynamic balancing of equipment on site, but also perform vibration detection and analysis.
A balancing machine is a device that can measure the imbalance of the equipment rotor. By performing balancing correction on the equipment rotor, the service life of the rotor and equipment can be extended several times, even tens or hundreds of times. Therefore, dynamic balancing of the rotor is very important. A balancing machine can achieve the allowable balance accuracy level of the rotor and also reduce the mechanical vibration amplitude generated by the rotor within the allowable range.
On site dynamic balancing instrument calibration is essential in current industrial use, and the technology of on-site balancing calibration has been widely applied in modern industry. Because the characteristics of on-site dynamic balance correction technology are very advantageous for many manufacturers. Fully understanding the characteristics of on-site dynamic balancing machine calibration technology enables us to better choose and use it.
Technical characteristics of on-site dynamic balancing instrument:
1. The on-site dynamic balancing instrument can achieve the effect of dynamic balancing without disassembling the rotor, which can effectively save downtime, manpower, and material resources. The entire process of on-site dynamic balancing calibration usually only takes about an hour to complete.
2. There are two types of on-site dynamic balancing instruments: double-sided dynamic balancing calibration and single-sided dynamic balancing calibration. However, double-sided dynamic balancing calibration is different from single-sided dynamic balancing calibration. When the diameter to width ratio of the rotor is less than twice, the double-sided dynamic balancing calibration method should be selected.
3. The rotor balance calibration can be implemented based on the actual working speed of the workpiece. When we disassemble the workpiece and calibrate it on the balancing machine, we cannot calibrate it in the high-speed gear. However, the on-site dynamic balancing instrument calibration can achieve high-speed rotation with a calibration speed of up to 60000 revolutions per minute.
4. Sometimes the vibration problem caused by the rotor may not be related to the rotor imbalance, so we can use an on-site dynamic balancing instrument to determine whether the vibration caused by the rotor is related to balance, which can avoid unnecessary balance correction.
5. In fact, there are many other factors that can affect rotor imbalance, such as clearances and angular deviations during rotor installation, which can also affect rotor imbalance. So we choose on-site dynamic balance correction to achieve a balanced state of the rotor, reducing vibration and damage to the equipment.
26 browse