What is the effect of rotor imbalance on motor quality? In this paper, the technicians of China Kezhi Creative Dynamic Balancer mainly analyze vibration and noise caused by mechanical unbalance of rotor, dynamic unbalance and static unbalance of rotor.
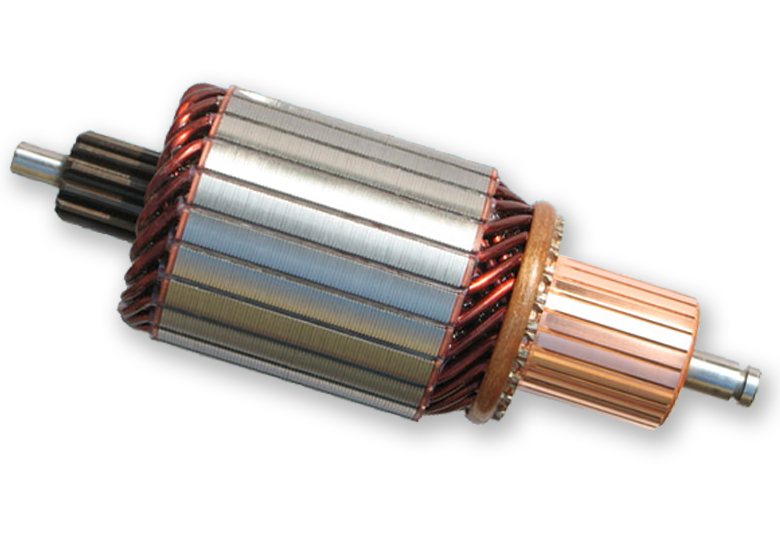
Generally, the imbalance of motor rotor can be divided into static imbalance, dynamic imbalance and hybrid imbalance. Centrifugal forces resulting from static imbalance produce equal-sized, phase-equal vibrations on both supports. The force coupling of centrifugal force caused by dynamic imbalance generates vibration of equal size and opposite phase on both supports. In practice, mixing imbalance is the most common one, which is caused by the combined action of residual static imbalance centrifugal force and dynamic imbalance centrifugal couple on two supports with different sizes and phases. The mechanical imbalance of the rotor can be eliminated by balancing.
1. Reasons for unbalanced vibration of rotor: residual unbalance during manufacture, large amount of dust adherence during long-term operation, shaft bending caused by thermal stress during operation, unbalanced load caused by thermal displacement of rotor parts, deformation or eccentricity caused by centrifugal force of rotor parts, shaft bending caused by external force (belt, gear, poor straight junction, etc.), and shaft bending or internal deformation caused by bad bearing device (precision or locking of shaft).
2. How to restrain rotor unbalance: Maintain the allowable unbalance, improve the over-tightness of shaft and core, improve the heterogeneity of thermal expansion and design. Improvement of strength design or assembly, modification of shaft strength design, modification of shaft coupling types and modification of straight connection centers, and prevention bias between bearing end face and shaft attachment or lock nut.
3. Causes of abnormal vibration and noise of bearings: internal damage of bearings, abnormal vibration of bearing axle direction, vibration of vibration system composed of axle direction spring constant and rotor mass; Cylindrical rolling bearings or large diameter high-speed ball bearings cause poor lubrication and bearing clearance.
4. Bearing replacement: proper shaft direction spring preload to change the bearing clearance, choose soft grease or excellent low temperature grease, make the residual clearance small (pay attention to the problem of temperature rise).
5. Rotor dynamic balance correction method: After dynamic balance measurement of rotor of dynamic balancing machine, the rotor can be balanced by weighting and de-weighting methods as required: so-called weighting method, i.e. correcting weight is added to the opposite direction of unbalance. Commonly used methods are welding, soldering, riveting, screw-tightening, weight-added block, etc. The weight removal method is to remove a certain amount of weight in the unbalanced direction. Commonly used methods are: boring, drilling, chipping, milling, grinding, etc.
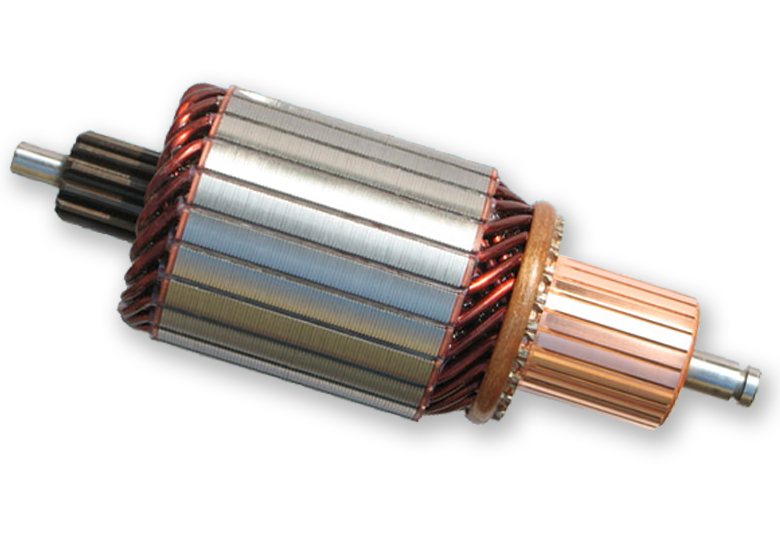
Generally, the imbalance of motor rotor can be divided into static imbalance, dynamic imbalance and hybrid imbalance. Centrifugal forces resulting from static imbalance produce equal-sized, phase-equal vibrations on both supports. The force coupling of centrifugal force caused by dynamic imbalance generates vibration of equal size and opposite phase on both supports. In practice, mixing imbalance is the most common one, which is caused by the combined action of residual static imbalance centrifugal force and dynamic imbalance centrifugal couple on two supports with different sizes and phases. The mechanical imbalance of the rotor can be eliminated by balancing.
1. Reasons for unbalanced vibration of rotor: residual unbalance during manufacture, large amount of dust adherence during long-term operation, shaft bending caused by thermal stress during operation, unbalanced load caused by thermal displacement of rotor parts, deformation or eccentricity caused by centrifugal force of rotor parts, shaft bending caused by external force (belt, gear, poor straight junction, etc.), and shaft bending or internal deformation caused by bad bearing device (precision or locking of shaft).
2. How to restrain rotor unbalance: Maintain the allowable unbalance, improve the over-tightness of shaft and core, improve the heterogeneity of thermal expansion and design. Improvement of strength design or assembly, modification of shaft strength design, modification of shaft coupling types and modification of straight connection centers, and prevention bias between bearing end face and shaft attachment or lock nut.
3. Causes of abnormal vibration and noise of bearings: internal damage of bearings, abnormal vibration of bearing axle direction, vibration of vibration system composed of axle direction spring constant and rotor mass; Cylindrical rolling bearings or large diameter high-speed ball bearings cause poor lubrication and bearing clearance.
4. Bearing replacement: proper shaft direction spring preload to change the bearing clearance, choose soft grease or excellent low temperature grease, make the residual clearance small (pay attention to the problem of temperature rise).
5. Rotor dynamic balance correction method: After dynamic balance measurement of rotor of dynamic balancing machine, the rotor can be balanced by weighting and de-weighting methods as required: so-called weighting method, i.e. correcting weight is added to the opposite direction of unbalance. Commonly used methods are welding, soldering, riveting, screw-tightening, weight-added block, etc. The weight removal method is to remove a certain amount of weight in the unbalanced direction. Commonly used methods are: boring, drilling, chipping, milling, grinding, etc.
238 browse